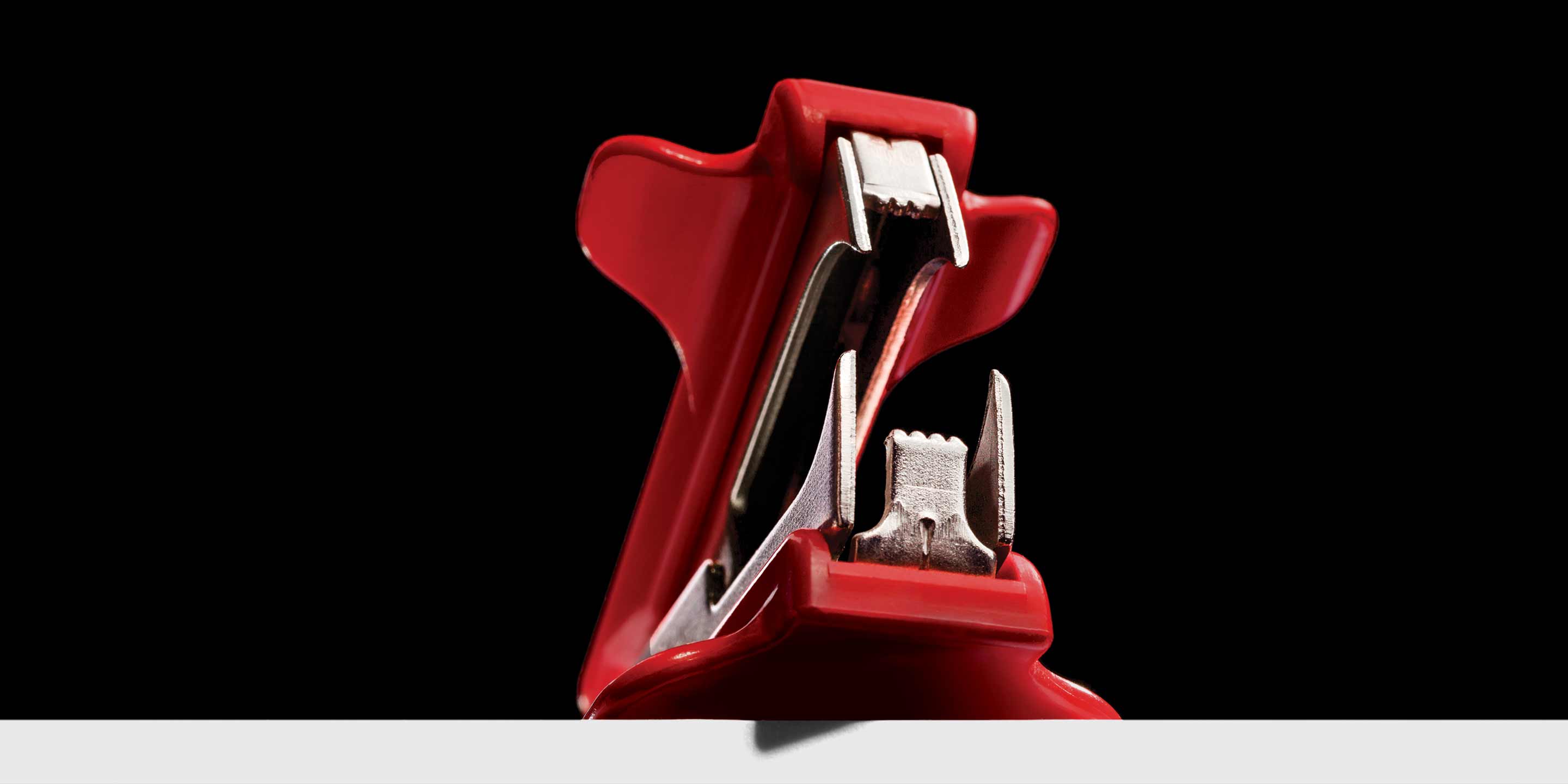
Setting a management target is an important step in any organization. The purpose of the objective is to give the organization the desired results. A strong objective describes what the company hopes to achieve and why. The objective gives employees a sense of direction and purpose. When the objective of an organization is clearly understood, it can be expressed in a measurable format.
Goals
A goal is an idea for the future, a desirable outcome. People often set deadlines to help them achieve their goals. They also make sure they measure progress against their goals when setting them. However, some goals can be elusive.
The success of a business depends on its ability to identify and define goals. These goals can serve many purposes and need to be shared by all levels of management. There are two types of goals: outcome-oriented goals and process-oriented goals. Outcome-oriented goal communicate the company's new vision and offer tangible changes for employees. However, process-oriented targets are similar to those that focus on outcomes but have a greater emphasis on new processes and workflows. The primary difference between process and outcome-oriented aims is that process-oriented aims are not always limited to a certain time frame.
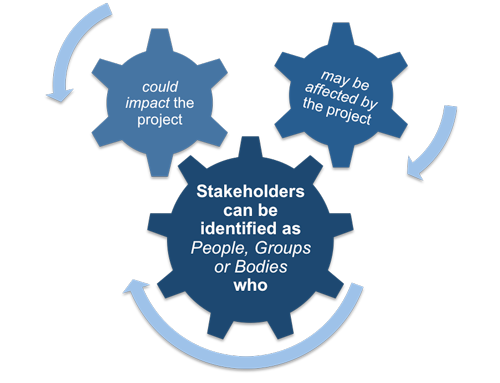
Purpose
The purpose of management is to make a firm or a business grow and become more successful. This can be achieved by proper planning and execution. Sound management is about producing better quality products and services at a low cost. Management also seeks to eliminate any form of waste in a business. Proper management also ensures that the supply of goods and services to people remains regular. This helps improve a company’s financial strength.
A good management team is dedicated to using resources efficiently, and this can be achieved by implementing logistic strategies and reducing wasteful processes. This can help companies achieve a greater profit margin. A management team will also be attentive to the needs of employees, and will develop procedures that will improve the working environment. Good management will place importance on the personal development and offer opportunities for internal promotion, training and mentoring.
Measurable form
An objective that is quantifiable can be described as a management goal. An objective to improve financial performance, for example, can be measured in terms of total sales, profitability and stock prices, among other factors. These measurements are critical to strategic planning, as they enable managers assess the direction of the business.
Management objectives must be quantifiable and specific. It should also relate to the organization's mission and contribute to that goal. It should be meaningful and easily measured.
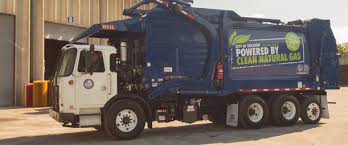
Setting objectives is a process
Management objectives refers to the process of establishing specific goals for an organisation. These objectives should be established by top management. They must be both measurable and flexible to change in the business environment. After the objectives have been established, the top management meets with the relevant groups to ensure their implementation. They then develop departmental targets, strategies, and action plans.
MBOs should be derived from the mission and vision of the company. They should be clearly communicated from top to bottom and should include everyone's input. Employees should also be encouraged to set their own objectives. This will empower them and give them more autonomy. To ensure that the company makes progress, it is important to set objectives.
FAQ
What's the difference between Six Sigma and TQM?
The key difference between the two quality management tools is that while six-sigma focuses its efforts on eliminating defects, total quality management (TQM), focuses more on improving processes and reducing cost.
Six Sigma stands for continuous improvement. This method emphasizes eliminating defects using statistical methods such p-charts, control charts, and Pareto analysis.
The goal of this method is to reduce variation in product output. This is done by identifying and correcting the root causes of problems.
Total quality management involves measuring and monitoring all aspects of the organization. Training employees is also part of total quality management.
It is commonly used as a strategy for increasing productivity.
What is TQM?
The industrial revolution was when companies realized that they couldn't compete on price alone. This is what sparked the quality movement. If they wanted to stay competitive, they needed to improve their quality and efficiency.
In response to this need for improvement, management developed Total Quality Management (TQM), which focused on improving all aspects of an organization's performance. It included continual improvement processes, employee involvement, customer satisfaction, and customer satisfaction.
What is the difference between leadership and management?
Leadership is about inspiring others. Management is all about controlling others.
A leader inspires followers while a manager directs workers.
A leader inspires others to succeed, while a manager helps workers stay on task.
A leader develops people; a manager manages people.
How do we build a culture that is successful in our company?
A successful company culture is one that makes people feel valued and respected.
It is founded on three basic principles:
-
Everyone has something valuable to contribute
-
People are treated fairly
-
Respect is shared between individuals and groups
These values reflect in how people behave. For example, they will treat others with courtesy and consideration.
They will be respectful of the opinions of other people.
They will also encourage others to share their ideas and feelings.
A company culture encourages collaboration and communication.
People are free to speak out without fear of reprisal.
They know that they will not be judged if they make mistakes, as long as the matter is dealt with honestly.
The company culture encourages honesty and integrity.
Everyone is aware that truth must be told.
Everyone recognizes that rules and regulations are important to follow.
No one is entitled to any special treatment or favors.
What are the 4 major functions of management
Management is responsible for organizing, managing, directing and controlling people, resources, and other activities. Management also involves setting goals and developing policies.
Organizations can achieve their goals through management. This includes leadership, coordination, control and motivation.
The four main functions of management are:
Planning - Planning involves determining what needs to be done.
Organizing is the act of deciding how things should go.
Directing – This means to get people to follow directions.
Controlling - This is the ability to control people and ensure that they do their jobs according to plan.
Statistics
- The BLS says that financial services jobs like banking are expected to grow 4% by 2030, about as fast as the national average. (wgu.edu)
- Hire the top business lawyers and save up to 60% on legal fees (upcounsel.com)
- This field is expected to grow about 7% by 2028, a bit faster than the national average for job growth. (wgu.edu)
- Your choice in Step 5 may very likely be the same or similar to the alternative you placed at the top of your list at the end of Step 4. (umassd.edu)
- The profession is expected to grow 7% by 2028, a bit faster than the national average. (wgu.edu)
External Links
How To
How can Lean Manufacturing be done?
Lean Manufacturing methods are used to reduce waste through structured processes. They were created by Toyota Motor Corporation in Japan in the 1980s. The goal was to produce quality products at lower cost. Lean manufacturing focuses on eliminating unnecessary steps and activities from the production process. It includes five main elements: pull systems (continuous improvement), continuous improvement (just-in-time), kaizen (5S), and continuous change (continuous changes). The production of only what the customer needs without extra work is called pull systems. Continuous improvement is constantly improving upon existing processes. Just-in–time refers when components or materials are delivered immediately to their intended destination. Kaizen refers to continuous improvement. It is achieved through small changes that are made continuously. Finally, 5S stands for sort, set in order, shine, standardize, and sustain. These five elements are combined to give you the best possible results.
The Lean Production System
Six key concepts underlie the lean production system.
-
Flow - focus on moving material and information as close to customers as possible;
-
Value stream mapping is the ability to divide a process into smaller tasks, and then create a flowchart that shows the entire process.
-
Five S's: Sort, Shine Standardize, Sustain, Set In Order, Shine and Shine
-
Kanban: Use visual signals such stickers, colored tape, or any other visual cues, to keep track your inventory.
-
Theory of Constraints - Identify bottlenecks in the process, and eliminate them using lean tools such kanban boards.
-
Just-in time - Get components and materials delivered right at the point of usage;
-
Continuous improvement is making incremental improvements to your process, rather than trying to overhaul it all at once.