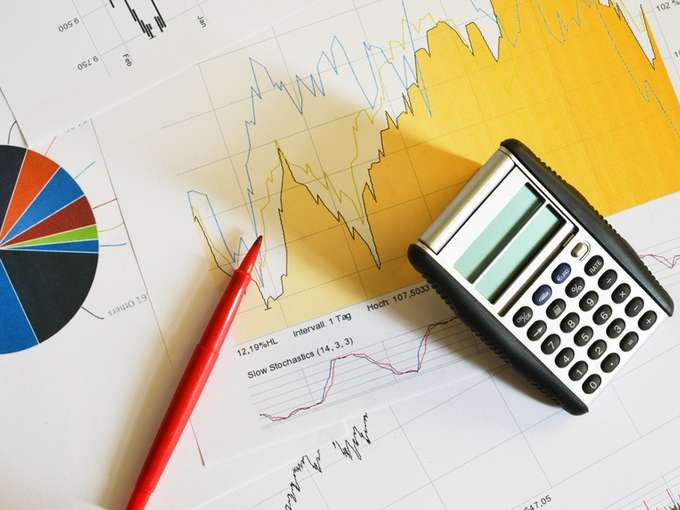
CSCMP stands for Certified Systems and Communications Manager, and it is a valuable certification for systems and communications professionals. CSCMP exam has 160 questions. It takes about four hours to complete. It is given by an independent 3rd-party company called Pearson VUE, and there are testing centers worldwide. The test is proctored in person and awards pass/fail status.
Academic membership
Academic membership in the CSCM is available to individuals in full-time academic positions at an accredited college or university. This membership is available for $175 per year and allows you to participate in collaborative forums as well as develop course content. Members can also network with colleagues in the field. Please contact us if interested in becoming a CSCM member.
Membership dues
The Council of Supply Chain Management Professionals is an organization dedicated to connecting, educating, and developing supply chain professionals around the globe. The group is $149 and you will have six months access to all the benefits and events that the organization offers. Young professionals can also sign up for a six-month membership for only $88. Both membership options expire on August 31, 2021.
CSCMP membership grants you access to many resources including surveys and research. These research results and actionable insights are available to members only. The organization also hosts webinars, which are free to members. CSCMP members can find out more information about supply chain management as well as how to improve your business operations.
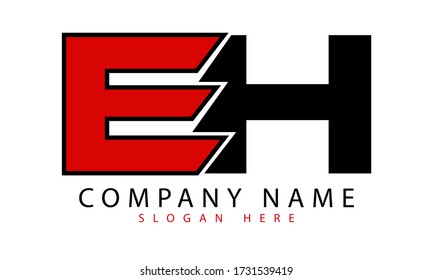
You can become a CSCMP member by taking the SCMP level two exam. You can take the exam within one year of submitting your membership fee. A confirmation email is sent approximately one week before the date of your test.
FAQ
What is a simple management tool that aids in decision-making and decision making?
A decision matrix is an easy but powerful tool to aid managers in making informed decisions. It helps them to think strategically about all options.
A decision matrix is a way to organize alternatives into rows and columns. It is easy to see how each option affects the other options.
We have four options in this example. They are represented by the boxes to the left of the matrix. Each box represents an option. The top row displays the current situation, and the bottom row shows what might happen if nothing is done.
The middle column shows the effect of choosing Option 1. It would translate into an increase in sales from $2million to $3million.
The effects of options 2 and 3 are shown in the next columns. These are positive changes - they increase sales by $1 million and $500 thousand respectively. These changes can also have negative effects. Option 2 increases the cost of goods by $100,000. Option 3 decreases profits and makes them less attractive by $200,000.
The last column displays the results of selecting Option 4. This results in a decrease of sales by $1,000,000
The best part about using a decision matrix to guide you is that you don’t need to keep track of which numbers go where. You just look at the cells and know immediately whether any given a choice is better than another.
The matrix has already done all of the work. It is as simple as comparing the numbers within the relevant cells.
Here is an example how you might use the decision matrix in your company.
Decide whether you want to invest more in advertising. If you do this, you will be able to increase revenue by $5000 per month. You'll also have additional expenses up to $10,000.
Look at the cell immediately below the one that states "Advertising" to calculate the net investment in advertising. It's $15,000. Advertising is a worthwhile investment because it has a higher return than the costs.
Six Sigma is so popular.
Six Sigma is easy to use and can lead to significant improvements. Six Sigma also gives companies a framework for measuring improvement and helps them focus on what is most important.
What is Six Sigma?
It's a method for quality improvement that focuses on customer service as well as continuous learning. The objective is to eliminate all defects through statistical methods.
Motorola created Six Sigma as part of their efforts to improve manufacturing processes in 1986.
It was quickly adopted by the industry and many companies are now using six-sigma to improve product design, production, delivery, customer service, and product design.
How does a manager motivate his/her employees?
Motivation is the desire to do well.
Enjoyable activities can motivate you.
Another way to get motivated is to see yourself as a contributor to the success of the company.
For example: If you want to be a doctor, you might find it more motivating seeing patients than reading medical books all day.
Another type of motivation comes from within.
Perhaps you have a strong sense to give back, for example.
Perhaps you enjoy working hard.
Ask yourself why you feel so motivated.
Then try to think about ways to change your situation to be more motivated.
What does Six Sigma mean?
Six Sigma employs statistical analysis to identify problems, measure them and analyze root causes. Six Sigma also uses experience to correct problems.
The first step is identifying the problem.
The data is then analyzed and collected to identify trends.
The problem can then be fixed by taking corrective measures.
Finally, data is reanalyzed to determine whether the problem has been eliminated.
This cycle continues until there is a solution.
What are the three main management styles you can use?
There are three main management styles: participative, laissez-faire and authoritarian. Each style has its advantages and disadvantages. Which style do you prefer? Why?
Autoritarian - The leader sets direction and expects everyone else to follow it. This style works best if the organization is large and stable.
Laissez-faire – The leader gives each individual the freedom to make decisions for themselves. This approach works best in small, dynamic organizations.
Participative: The leader listens to everyone's ideas and suggestions. This style is best for small organizations where everyone feels valued.
Statistics
- This field is expected to grow about 7% by 2028, a bit faster than the national average for job growth. (wgu.edu)
- The profession is expected to grow 7% by 2028, a bit faster than the national average. (wgu.edu)
- Hire the top business lawyers and save up to 60% on legal fees (upcounsel.com)
- UpCounsel accepts only the top 5 percent of lawyers on its site. (upcounsel.com)
- 100% of the courses are offered online, and no campus visits are required — a big time-saver for you. (online.uc.edu)
External Links
How To
How can you implement the Kaizen technique?
Kaizen means continuous improvement. The term was coined in the 1950s at Toyota Motor Corporation and refers to the Japanese philosophy emphasizing constant improvement through small incremental changes. It's a team effort to continuously improve processes.
Kaizen is one the most important methods of Lean Manufacturing. This concept requires employees to identify and solve problems during manufacturing before they become major issues. This is how you can improve the quality and lower the cost.
The main idea behind kaizen is to make every worker aware of what happens around him/her. To prevent problems from happening, any problem should be addressed immediately. Report any problem you see at work to your manager.
Kaizen follows a set of principles. We always start from the end product and move toward the beginning. To improve our factory, for example, we need to fix the machines that produce the final product. Next, we repair the machines that make components. Then, the machines that make raw materials. Then, we fix those who work directly with the machines.
This approach is called 'kaizen' because it focuses on improving everything steps by step. Once we have finished fixing the factory, we return to the beginning and work until perfection.
To implement kaizen in your business, you need to find out how to measure its effectiveness. There are several ways to determine whether kaizen is working well. Another way to determine if kaizen is working well is to look at the quality of the products. Another way is to see how much productivity has increased since implementing kaizen.
Another way to know whether kaizen is working is to ask yourself why did you decide to implement kaizen. You were trying to save money or obey the law? It was a way to save money or help you succeed.
Let's say you answered yes or all of these questions. Congratulations! Now you're ready for kaizen.