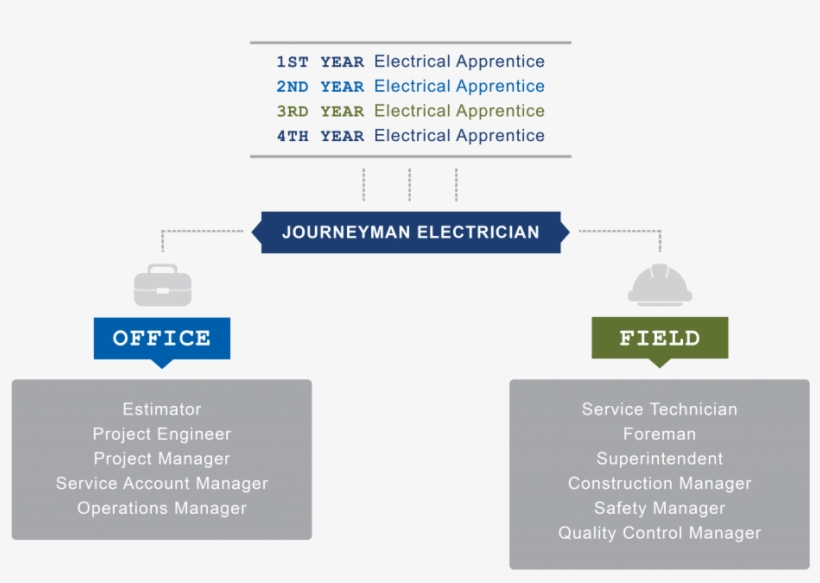
Training in change management is strategic. It helps leaders guide their teams through transitions, educates employees, and increases the organization's success rates. Additionally, change management training is a great way to increase employee satisfaction and productivity. To learn more, download our eBook: Change Management Training - 5 Strategies to Boost Employee Engagement and Productivity
Effective change management training is a strategic skill
It is a crucial strategic skill to manage change. You must be able design and deliver training sessions that are effective. Even though one-day trainings may not prove effective, small, asynchronous sessions which combine live training with job aids or reference materials can prove to be more successful. These methods allow organizations to quickly adapt to changing circumstances. This article will share some of the best practices to ensure that your training sessions meet the needs.
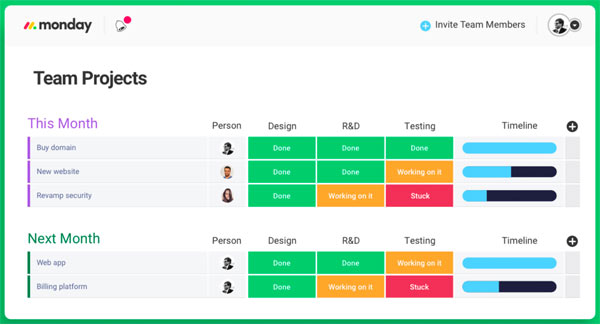
It helps leaders guide their teams through change
The combination of people and technical skills is essential for change management. Along with technical skills, leaders must also be sensitive and understanding of the feelings of others. Communication must not only be effective but also genuine. Leaders should show concern and reassurance if employees feel anxious or mistrustful. Speaking without action will likely result in distrust. A leader should be a role model and act as a role model. Employees need to feel ownership over the changes.
It helps employees to understand the changes.
It is essential to explain in detail the changes that employees will be facing during change management training. Change management training must make it easy for employees to grasp the changes and be useful in their job. To ensure that employees understand the changes occurring, it is important to repeat this training throughout the training. To make sure employees are familiar with the changes, a formal statement should be given during training.
It increases success rates of an organization
Change management is a skill that enables employees to perform their jobs and learn to accept changes. This training often focuses on specific technologies, organizational structures, or overall business strategies. The training program will vary depending on what organization it is. But it is vital to provide employees with a foundation for change. Below are some important steps to take to provide your employees with the skills needed to effectively manage change.
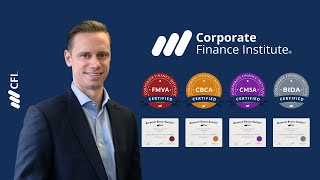
It prepares people to handle change.
Change management training helps employees accept, implement, as well as perform their jobs with respect to change. It helps them to understand how and why changes happen and to devise better strategies to implement them. By introducing change management training, individuals will become better champions for new products or services. This will increase their commitment, and allow them to adapt to new changes. This helps them to stay engaged. They will be better equipped to manage change.
FAQ
What is Six Sigma?
It is a way to improve quality that places emphasis on customer service and continuous learning. It is a method that eliminates defects using statistical techniques.
Motorola invented Six Sigma in 1986 as part its efforts to improve manufacturing.
The idea spread quickly throughout the industry, and today, many organizations are using six sigma methods to improve product design, production, delivery, and customer service.
How can a manager improve his/her managerial skills?
Through demonstrating good management skills at every opportunity
Managers must continuously monitor the performance levels of their subordinates.
You should immediately take action if you see that your subordinate is not performing as well as you would like.
You should be able pinpoint what needs to improve and how to fix it.
What are the 4 major functions of management
Management is responsible for planning, organizing, directing, and controlling people and resources. This includes setting goals, developing policies and procedures, and creating procedures.
Management aids an organization in reaching its goals by providing direction and coordination, control, leadership motivation, supervision, training, evaluation, and leadership.
These are the four major functions of management:
Planning - Planning is about determining what must be done.
Organizing - Organizing involves deciding how things should be done.
Directing - Directing is when you get people to do what you ask.
Controlling - Controlling means ensuring that people carry out tasks according to plan.
What kind of people use Six Sigma
People who have worked with statistics and operations research will usually be familiar with the concepts behind six sigma. It can be used by anyone in any business aspect.
Because it requires a high level of commitment, only those with strong leadership skills will make an effort necessary to implement it successfully.
How do we create a company culture that is productive?
A successful company culture is one that makes people feel valued and respected.
It's founded on three principal principles:
-
Everybody can contribute something valuable
-
People are treated fairly
-
It is possible to have mutual respect between groups and individuals
These values can be seen in the behavior of people. They will treat others with consideration and courtesy.
They will respect the opinions of others.
They will also encourage others to share their ideas and feelings.
A company culture encourages collaboration and communication.
People can freely express their opinions without fear or reprisal.
They are aware that mistakes can be accepted if they are treated honestly.
The company culture promotes honesty, integrity, and fairness.
Everyone is aware that truth must be told.
Everyone understands there are rules that they must follow.
No one is entitled to any special treatment or favors.
What are the main styles of management?
The three basic management styles are: authoritarian, laissez-faire, and participative. Each style has its own strengths and weaknesses. Which style do YOU prefer? Why?
Authoritarian – The leader sets a direction and expects everyone follows it. This style is best when the organization has a large and stable workforce.
Laissez-faire – The leader gives each individual the freedom to make decisions for themselves. This style works best when an organization is small and dynamic.
Participative - Leaders listen to all ideas and suggestions. This style works best in smaller organizations where everyone feels valued.
What are your main management skills
Managerial skills are crucial for every business owner, regardless of whether they run a small store in their locality or a large corporation. They include the ability to manage people, finances, resources, time, and space, as well as other factors.
You will need management skills to set goals and objectives, plan strategies, motivate employees, resolve problems, create policies and procedures, and manage change.
As you can see, there's no end to the list of managerial duties!
Statistics
- The profession is expected to grow 7% by 2028, a bit faster than the national average. (wgu.edu)
- 100% of the courses are offered online, and no campus visits are required — a big time-saver for you. (online.uc.edu)
- The BLS says that financial services jobs like banking are expected to grow 4% by 2030, about as fast as the national average. (wgu.edu)
- This field is expected to grow about 7% by 2028, a bit faster than the national average for job growth. (wgu.edu)
- Hire the top business lawyers and save up to 60% on legal fees (upcounsel.com)
External Links
How To
How is Lean Manufacturing done?
Lean Manufacturing processes are used to reduce waste and improve efficiency through structured methods. They were created in Japan by Toyota Motor Corporation during the 1980s. The primary goal was to make products with lower costs and maintain high quality. Lean manufacturing focuses on eliminating unnecessary steps and activities from the production process. It is composed of five fundamental elements: continuous improvement; pull systems, continuous improvements, just-in–time, kaizen, continuous change, and 5S. Pull systems are able to produce exactly what the customer requires without extra work. Continuous improvement is constantly improving upon existing processes. Just-intime refers the time components and materials arrive at the exact place where they are needed. Kaizen means continuous improvement. Kaizen involves making small changes and improving continuously. Five-S stands for sort. It is also the acronym for shine, standardize (standardize), and sustain. These five elements are combined to give you the best possible results.
The Lean Production System
Six key concepts form the foundation of the lean production system:
-
Flow is about moving material and information as near as customers can.
-
Value stream mapping- This allows you to break down each step of a process and create a flowchart detailing the entire process.
-
Five S's – Sort, Put In Order Shine, Standardize and Sustain
-
Kanban: Use visual signals such stickers, colored tape, or any other visual cues, to keep track your inventory.
-
Theory of constraints - identify bottlenecks in the process and eliminate them using lean tools like kanban boards;
-
Just-in-time delivery - Deliver components and materials right to your point of use.
-
Continuous improvement is making incremental improvements to your process, rather than trying to overhaul it all at once.