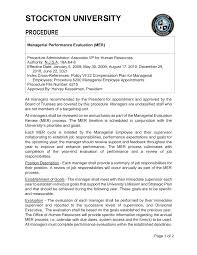
The supply chain webinars are a great way learn about current trends and how they can impact your business. Many are open to all and free of charge. Learn more about Supply Chain Management. AI, and Machine Learning. Some even touch on Industry 4.0 technologies and Multiparty control towers. These free events are great for business leaders or anyone just interested in learning more about supply chain technology.
Machine Learning
Machine Learning can be applied to your supply chain in many different ways. It can help optimize factory schedules, balance make-to-order/made-to-stock workflows, prevent material delays in production, and more. Machine learning can also help detect fraud. It analyzes real-time data and looks for anomalies and pattern deviations, notifying supply chain managers of possible problems.
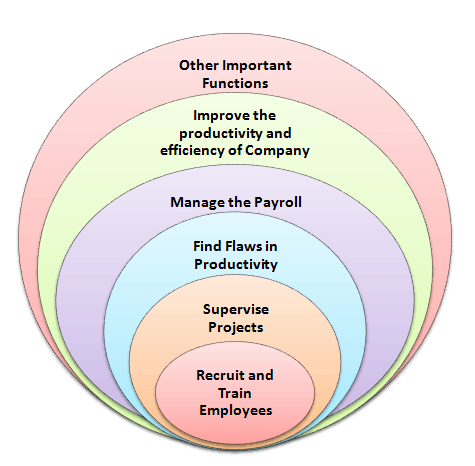
AI
Predictive Analytics is a great tool to improve supply chain efficiency. But, it can be challenging to interpret the data generated from this technology. This webinar will help supply chain managers understand the basics of AI and how to apply it to their business.
Industry 4.0 technologies
Industry 4.0 technologies, otherwise known as the digital supply chain, are a major shift in the way businesses conduct business. It is hard to identify the competitive advantages from new technologies given the pace of change. This Capstone Webinar will help you understand the change agents and key domains that drive the transformation. The webinar will also address some of the most common questions about key technologies.
Multiparty control towers
Multiparty control Towers are an essential part of the supply-chain ecosystem. They allow companies to automate repetitive tasks and reduce time and cost. Multiparty control towers are a powerful tool when combined with orchestration platform. These solutions can link all parts of the supply chain ecosystem. They provide a single source to truth for all those involved.
Collaboration within the supply chain
Collaboration within the supply-chain is becoming more popular. This strategy can be a great way to increase a company’s bottomline. Collaboration can not only improve operational efficiency but also foster innovation and better risk management. Collaboration can occur in both vertical and horizontal dimensions. However, there are key factors to be aware of.
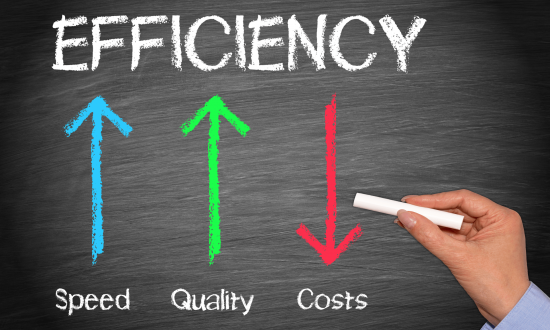
The future of the supply chain
The webinars on the Future of the Supply Chain address issues that affect supply chains. They examine how to make supply chains more sustainable, integrate corporate Governance into value chains, improve availability of medical devices for consumers, and make them more sustainable. They will also discuss the ways in which to manage increasing antitrust and ESG convergence. The session will include trends in supply chain from 2022 onwards.
FAQ
It seems so difficult sometimes to make sound business decisions.
Complex systems and many moving parts make up businesses. The people who run them must juggle multiple priorities at once while also dealing with uncertainty and complexity.
Understanding the impact of these factors on the system is crucial to making sound decisions.
It is important to consider the functions and reasons for each part of the system. You then need to consider how those individual pieces interact with each other.
Also, you should ask yourself if there have been any assumptions in your past behavior. If you don't have any, it may be time to revisit them.
For help, ask someone else if you're still stumped after all the above. You may be able to see things from a different perspective than you are and gain insight that can help you find a solution.
What is the role of a manager in a company?
The role of a manager varies from one industry to another.
In general, a manager controls the day-to-day operations of a company.
He/she ensures the company meets its financial commitments and produces goods/services that customers demand.
He/she makes sure that employees adhere to the rules and regulations as well as quality standards.
He/she oversees marketing campaigns and plans new products.
What's the difference between Six Sigma and TQM?
The main difference in these two quality management tools lies in the fact that six sigma is focused on eliminating defects and total quality management (TQM), emphasizes improving processes and reducing costs.
Six Sigma can be described as a strategy for continuous improvement. It emphasizes the elimination and improvement of defects using statistical methods, such as control charts, P-charts and Pareto analysis.
This method aims to reduce variation in product production. This is done by identifying root causes and rectifying them.
Total quality management refers to the monitoring and measurement of all aspects in an organization. Training employees is also part of total quality management.
It is commonly used as a strategy for increasing productivity.
What is TQM and how can it help you?
The industrial revolution led to the birth and growth of the quality movement. Manufacturing companies realized they couldn't compete solely on price. If they wanted to stay competitive, they needed to improve their quality and efficiency.
Management realized the need to improve and created Total Quality Management, which focused on improving all aspects within an organization's performance. It included continual improvement processes, employee involvement, customer satisfaction, and customer satisfaction.
What is a management tool to help with decision-making?
A decision matrix is a simple but powerful tool for helping managers make decisions. It helps them think systematically about all the options available to them.
A decision matrix is a way of representing alternatives as rows and columns. This allows one to see how each alternative impacts other options.
We have four options in this example. They are represented by the boxes to the left of the matrix. Each box represents one option. The top row shows the status quo (the current situation), and the bottom row shows what would happen if nothing was done at all.
The middle column displays the impact of selecting Option 1. It would translate into an increase in sales from $2million to $3million.
The effects of options 2 and 3 are shown in the next columns. These are positive changes - they increase sales by $1 million and $500 thousand respectively. But, they also have some negative consequences. Option 2 increases the cost of goods by $100,000. Option 3 decreases profits and makes them less attractive by $200,000.
The last column shows you the results of Option 4. This will result in sales falling by $1,000,000
The best thing about a decision matrix is the fact that you don't have to remember which numbers go with what. It's easy to see the cells and instantly know if any one of them is better than another.
The matrix already does all the work. It's simply a matter of comparing the numbers in the relevant cells.
Here's an example showing how you might use a Decision Matrix in your business.
You want to decide whether or not to invest more money into advertising. If you do this, you will be able to increase revenue by $5000 per month. However, this will mean that you'll have additional expenses of $10,000.
The net result of advertising investment can be calculated by looking at the cell below that reads "Advertising." It is 15 thousand. Advertising is worth more than its cost.
What are some common management mistakes?
Sometimes, managers make their job more difficult than it is.
They may not be able to delegate enough responsibility to staff or provide adequate support.
In addition, many managers lack the communication skills required to motivate and lead their teams.
Managers can set unrealistic expectations for their employees.
Some managers may try to solve every problem themselves instead of delegating responsibility to others.
Statistics
- UpCounsel accepts only the top 5 percent of lawyers on its site. (upcounsel.com)
- The average salary for financial advisors in 2021 is around $60,000 per year, with the top 10% of the profession making more than $111,000 per year. (wgu.edu)
- The BLS says that financial services jobs like banking are expected to grow 4% by 2030, about as fast as the national average. (wgu.edu)
- The profession is expected to grow 7% by 2028, a bit faster than the national average. (wgu.edu)
- Hire the top business lawyers and save up to 60% on legal fees (upcounsel.com)
External Links
How To
How do I do the Kaizen Method?
Kaizen means continuous improvement. The term was coined in the 1950s at Toyota Motor Corporation and refers to the Japanese philosophy emphasizing constant improvement through small incremental changes. It's a process where people work together to improve their processes continuously.
Kaizen is one of the most effective methods used in Lean Manufacturing. In this concept, employees who are responsible for the production line must identify problems that exist during the manufacturing process and try to solve them before they become big issues. This way, the quality of products increases, and the cost decreases.
Kaizen is the idea that every worker should be aware of what is going on around them. To prevent problems from happening, any problem should be addressed immediately. So, if someone notices a problem while working, he/she should report it to his/her manager.
Kaizen follows a set of principles. Start with the end product, and then move to the beginning. In order to improve our factory's production, we must first fix the machines producing the final product. Next, we fix the machines which produce components. Finally, we repair the workers who are directly involved with these machines.
This method, called 'kaizen', focuses on improving each and every step of the process. Once the factory is fixed, we return to the original site and work our way back until we get there.
How to measure kaizen's effectiveness in your business is essential to implement it. There are several ways that you can tell if your kaizen system is working. Another way to determine if kaizen is working well is to look at the quality of the products. Another way to find out how productive your company has been since you implemented kaizen is to measure the increase in productivity.
If you want to find out if your kaizen is actually working, ask yourself why. It was because of the law, or simply because you wanted to save some money. It was a way to save money or help you succeed.
Suppose you answered yes to any of these questions, congratulations! You're now ready to get started with kaizen.