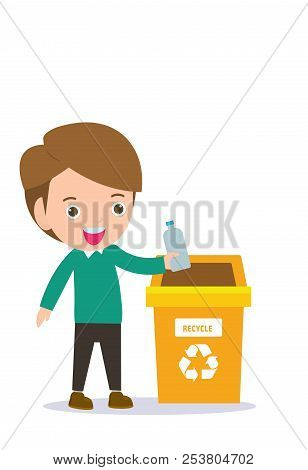
A compliance job may appeal to those with a background in finance, law, or any other related fields. These entry-level positions give you practical experience and provide exposure to compliance regulations. Employers prefer to hire qualified candidates, even though a professional certificate is not necessary. Most certifications require specific courses as well as continuing education credits. Certifications are useful for keeping your compliance skills current.
Experience in a related industry
It is essential to have relevant experience if you are looking for a job in compliance. As a paralegal for example, it's possible to gain valuable insights by working in a back office. Experience in a related industry is also a good starting point.
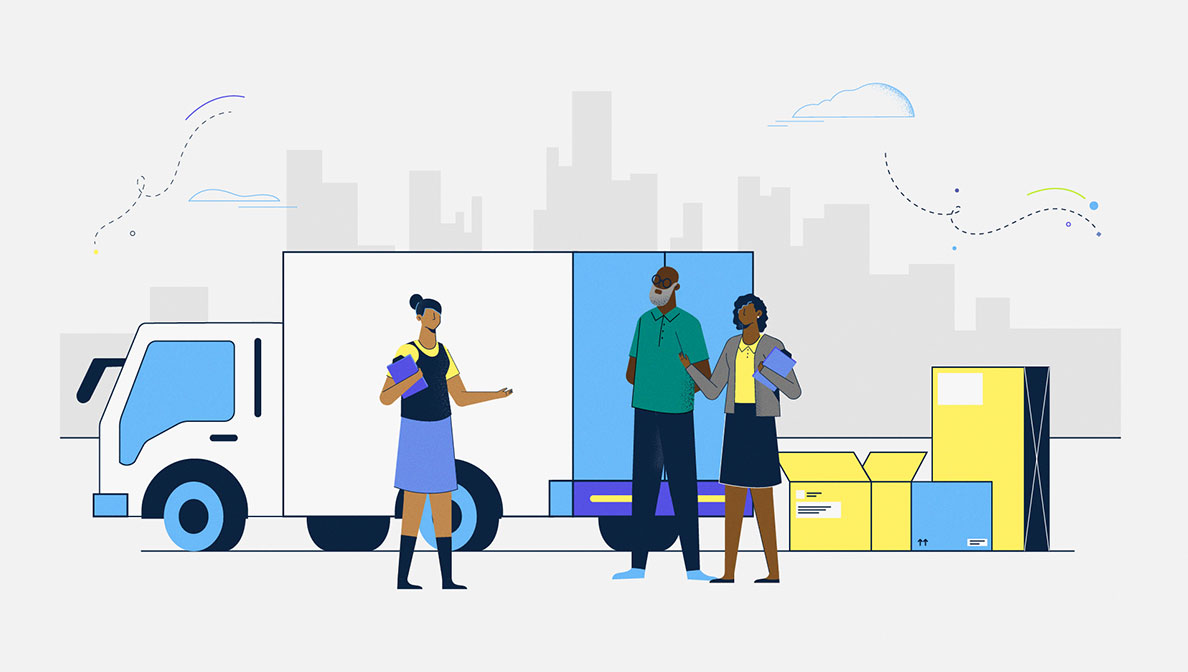
You should also have leadership experience. To be successful in a job as a compliance officer, you need to be able manage a team, take initiative, and communicate effectively and efficiently with both internal and externe stakeholders. A strong analytical, quantitative, or oral communication skill is essential.
Salary
The salary of a compliance manager is determined by many factors. It is important to consider the location, education, experience and whereabouts when determining the salary for a compliance manager. Robert Half, an industry leader in salary research, projects that a compliance chief will earn $209,000 by 2022. This represents a 1.5% increase on the previous year.
Hedge funds, banks, and other big brands are often the top-paying jobs in compliance. As such, they often have a competitive base pay and great bonus potential. Compliance jobs at fintech companies are becoming increasingly attractive due to the availability of share options and flexibility outside of work.
Responsibilities
There are many responsibilities associated with compliance jobs. These include managing a compliance program and writing and implementing company policies. No matter what job they hold, compliance managers should have a solid understanding of legal and regulatory issues. They will be responsible for advising both employees and managers on these issues. They can also help to identify potential violations and conduct investigations.
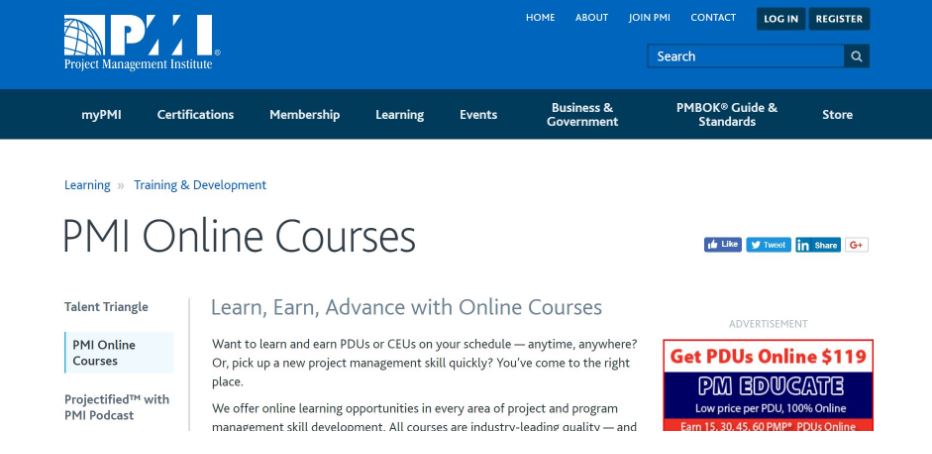
Compliance professionals usually move quickly through the ranks. In as little as two to four year, they can move from being junior compliance officers to being senior officers. Eventually, they may progress to compliance managers and senior management, which require at least five years of experience. In large corporate organizations, compliance careers typically follow a linear progression. An analyst might move up to become an associate vice-president, and then vice-president in a large company. A manager or senior manager may have the responsibility for compliance in smaller companies.
FAQ
What are your main management skills
No matter if they are running a local business or an international one, management skills are vital. They are the ability to manage people and finances, space, money, and other factors.
Managerial skills are required when setting goals and objectives and planning strategies, leading employees, motivating them, solving problems, creating policies, procedures, or managing change.
As you can see there is no end to the number of managerial tasks.
What are the five management processes?
Planning, execution, monitoring and review are the five stages of any business.
Planning means setting goals for the long-term. It includes defining what you want to achieve and how you plan to do it.
Execution takes place when you actually implement the plans. These plans must be adhered to by everyone.
Monitoring is the process of evaluating your progress toward achieving your objectives. Regular reviews of performance against targets, budgets, and other goals should be part.
Review events take place at each year's end. They allow for an assessment of whether all went well throughout the year. If not there are changes that can be made to improve the performance next year.
After each year's review, evaluation occurs. It helps identify which aspects worked well and which didn't. It also provides feedback regarding how people performed.
What do we mean when we say "project management"?
We mean managing the activities involved in carrying out a project.
This includes defining the scope, identifying the requirements and preparing the budget. We also organize the project team, schedule the work, monitor progress, evaluate results, and close the project.
What are some common mistakes managers make when managing people?
Sometimes managers make their job harder than they need to.
They might not give enough support and delegate the right responsibilities to their staff.
Many managers lack the communication skills to motivate and lead their employees.
Managers can set unrealistic expectations for their employees.
Managers may choose to solve every problem all by themselves, instead of delegating to others.
What are the 3 basic management styles?
The three major management styles are authoritarian (left-faire), participative and laissez -faire. Each style has its advantages and disadvantages. Which style do YOU prefer? Why?
Authority - The leader is the one who sets the direction and expects everyone in the organization to follow it. This style is best when the organization has a large and stable workforce.
Laissez-faire – The leader gives each individual the freedom to make decisions for themselves. This approach works best in small, dynamic organizations.
Participative: The leader listens to everyone's ideas and suggestions. This style works best in smaller organizations where everyone feels valued.
What's the difference between Six Sigma and TQM?
The major difference between the two tools for quality management is that six Sigma focuses on eliminating defect while total quality control (TQM), on improving processes and decreasing costs.
Six Sigma stands for continuous improvement. It emphasizes the elimination and improvement of defects using statistical methods, such as control charts, P-charts and Pareto analysis.
The goal of this method is to reduce variation in product output. This is done by identifying root causes and rectifying them.
Total quality management is the measurement and monitoring of all aspects within an organization. Training employees is also part of total quality management.
It is commonly used as a strategy for increasing productivity.
Statistics
- UpCounsel accepts only the top 5 percent of lawyers on its site. (upcounsel.com)
- The profession is expected to grow 7% by 2028, a bit faster than the national average. (wgu.edu)
- 100% of the courses are offered online, and no campus visits are required — a big time-saver for you. (online.uc.edu)
- As of 2020, personal bankers or tellers make an average of $32,620 per year, according to the BLS. (wgu.edu)
- Our program is 100% engineered for your success. (online.uc.edu)
External Links
How To
What is Lean Manufacturing?
Lean Manufacturing processes are used to reduce waste and improve efficiency through structured methods. They were created by Toyota Motor Corporation in Japan in the 1980s. The aim was to produce better quality products at lower costs. Lean manufacturing emphasizes removing unnecessary steps from the production process. It is made up of five elements: continuous improvement, continuous improvement, just in-time, continuous change, and 5S. The production of only what the customer needs without extra work is called pull systems. Continuous improvement is constantly improving upon existing processes. Just-in-time is when components and other materials are delivered at their destination in a timely manner. Kaizen refers to continuous improvement. It is achieved through small changes that are made continuously. The 5S acronym stands for sort in order, shine standardize and maintain. These five elements are used together to ensure the best possible results.
Lean Production System
The lean production system is based on six key concepts:
-
Flow - focuses on moving information and materials as close to customers as possible.
-
Value stream mapping - break down each stage of a process into discrete tasks and create a flowchart of the entire process;
-
Five S's: Sort, Shine Standardize, Sustain, Set In Order, Shine and Shine
-
Kanban - use visual signals such as colored tape, stickers, or other visual cues to keep track of inventory;
-
Theory of constraints: identify bottlenecks in your process and eliminate them using lean tools, such as kanban board.
-
Just-in Time - Send components and material directly to the point-of-use;
-
Continuous improvement - Make incremental improvements rather than overhauling the entire process.