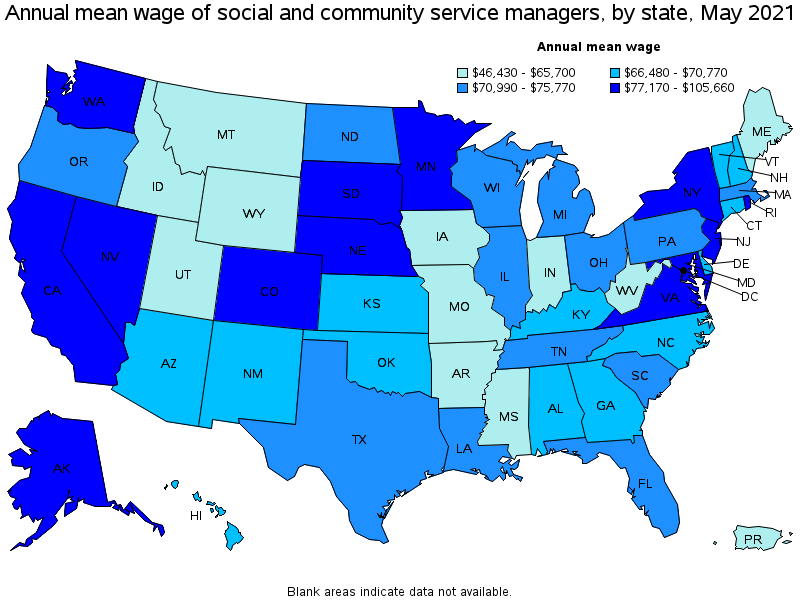
SCOR models are used in supply-chain management. It is divided into Levels, which are the levels of the model. Level one relates to the Make process. Level 2 is broken down into three sub-processes. Each sub-process has its own special tag that represents the beginning of the process. The child-related tags are identified by a number, which represents a scenario. In addition, there are four different types of references, which are the Reference components and the Prescriptive analytics framework.
Levels of SCOR model
SCOR is a model that combines concepts of measurement, benchmarking, and reengineering. It creates a comprehensive view of business processes. It provides a standardized approach to supply chain evaluation and identifies areas for improvement. The model can be used by any industry with a supply chain. The first step in the project is to determine the scope, context, geographies and key components.
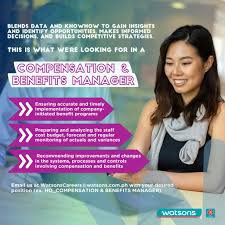
SCOR Model addresses multiple industries, focusing on services, products, and transactions. The basic framework is source, make, deliver, and return. This model may be useful, but it can lose its value if the purpose, strategic alignment, as well as operational excellence are unclear. A business context study focuses on the current performance of an organization in relation to customers and other businesses. It also helps to identify conformance gaps. It is important to use tools like SWOT Analysis, Benchmarking and Value Stream Mapping in order to conduct a business context analysis.
The four pillars of supply chain management
Supply-chain management should be in sync with the company’s strategy, financial and service factors. These four areas will help companies build confidence in their handling of the entire supply chain process. The four pillars of supply chain management include product integrity, quality, capability, and fraud. In order to make supply-chain management successful, companies need to align these areas with their business goals.
Planning and implementation of supply-chain processes are vital components. Companies can reduce their inventory costs and avoid shortfalls by managing it well. Effective supply chains require qualified purchasing personnel that are skilled in managing and maintaining inventory. A company without qualified personnel will either overbuy raw materials, or run out, which can lead to financial strain. A company's success is dependent on its supply chain.
Framework for predictive analytics
A predictive analytics framework is a set of algorithms that allows computers to make predictions based on statistical data relationships. Examples of predictive analytics algorithms are Bayes classifier and ID3, which structure graphs of potential outcomes from a dataset. Predictive analysis is about creating a model from past data that can predict future results. AI and predictive analytics are tools that help companies predict future results or predict customer behavior.
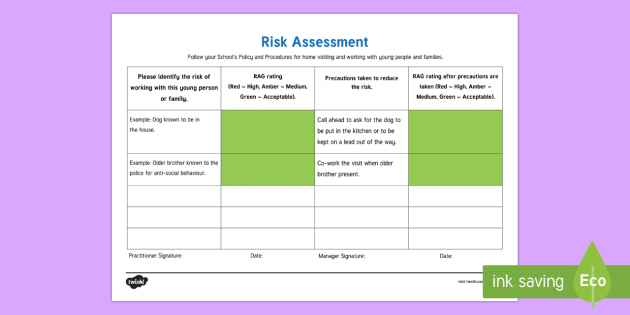
This method makes use of machine-learning algorithms to process large amounts of data and make recommendations based upon specific requirements. However, these algorithms are not as accurate as human judgment and will still require human discernment. Prescriptive analysis can be extremely helpful for businesses, especially in sales. Based on their data, predictive analytics algorithms can assist salespeople in making more informed decisions. Marketers can use trends to tailor their strategies and tactics to customers' behavior by using predictive analytics algorithms.
FAQ
What is the main difference between Six Sigma Six Sigma TQM and Six Sigma Six Sigma?
The major difference between the two tools for quality management is that six Sigma focuses on eliminating defect while total quality control (TQM), on improving processes and decreasing costs.
Six Sigma can be described as a strategy for continuous improvement. It emphasizes the elimination or minimization of defects through statistical methods such control charts and p charts.
This method aims to reduce variation in product production. This is achieved by identifying and addressing the root causes of problems.
Total quality management is the measurement and monitoring of all aspects within an organization. Training employees is also part of total quality management.
It is frequently used as an approach to increasing productivity.
What role does a manager play in a company?
Managers' roles vary from industry to industry.
A manager is generally responsible for overseeing the day to day operations of a company.
He/she will ensure that the company fulfills its financial obligations.
He/she will ensure that employees follow all rules and regulations, and adhere to quality standards.
He/she designs new products or services and manages marketing campaigns.
How do you manage employees effectively?
Effectively managing employees means making sure they are productive and happy.
This also involves setting clear expectations and monitoring their performance.
To do this successfully, managers need to set clear goals for themselves and for their teams.
They must communicate clearly with their staff. They must communicate clearly with staff members.
They also need to keep records of their team's activities. These include:
-
What was the result?
-
How much work were you able to accomplish?
-
Who did it, anyway?
-
It was done!
-
Why?
This data can be used to evaluate and monitor performance.
Statistics
- Hire the top business lawyers and save up to 60% on legal fees (upcounsel.com)
- UpCounsel accepts only the top 5 percent of lawyers on its site. (upcounsel.com)
- 100% of the courses are offered online, and no campus visits are required — a big time-saver for you. (online.uc.edu)
- Your choice in Step 5 may very likely be the same or similar to the alternative you placed at the top of your list at the end of Step 4. (umassd.edu)
- Our program is 100% engineered for your success. (online.uc.edu)
External Links
How To
How can you use the Kaizen method?
Kaizen means continuous improvement. This term was first used by Toyota Motor Corporation in the 1950s. It refers to the Japanese philosophy that emphasizes continuous improvement through small incremental changes. It is a process where people come together to improve their processes.
Kaizen is one of the most effective methods used in Lean Manufacturing. The concept involves employees responsible for manufacturing identifying problems and trying to fix them before they become serious issues. This improves the quality of products, while reducing the cost.
Kaizen is an approach to making every worker aware and alert to what is happening around them. Correct any errors immediately to avoid future problems. If someone spots a problem while at work, they should immediately report it to their manager.
There are some basic principles that we follow when doing kaizen. Always start with the end product in mind and work our way back to the beginning. To improve our factory, for example, we need to fix the machines that produce the final product. Next, we fix the machines which produce components. And finally, we fix the workers who work directly with those machines.
This method, called 'kaizen', focuses on improving each and every step of the process. Once the factory is fixed, we return to the original site and work our way back until we get there.
Before you can implement kaizen into your business, it is necessary to learn how to measure its effectiveness. There are many ways you can determine if kaizen has been implemented well. Another method is to see how many defects are found on the products. Another way is determining how much productivity increased after implementing kaizen.
You can also find out if kaizen works by asking yourself why you decided to implement it. Did you do it because it was legal or to save money? Did you really think that it would help you achieve success?
Let's say you answered yes or all of these questions. Congratulations! You're now ready to get started with kaizen.