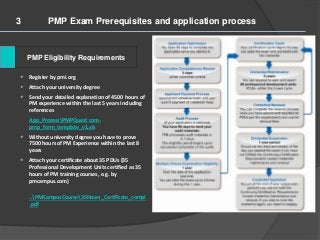
Proper waste management must always be taken into consideration when managing chemical waste or manufactured waste. Incompatible chemicals should be stored in separate secondary containment bins to prevent the formation of toxic fumes and aerosols. Additionally, incompatible chemicals should not be mixed with other chemicals, which may cause explosions and fires.
Hazards
To prevent environmental and health hazards, chemicals must be properly disposed. Proper disposal requires identifying which chemical waste streams should be disposed. This is typically done at the end of an experiment or protocol. Sometimes hazardous wastes are mixed with normal waste to make money. This is not an option.
Before you store hazardous chemicals, make sure you have the MSDS of all chemicals you use. These MSDSs are often online or available from the manufacturer. These include the hazard information for a chemical, as well as its composition. In addition, they contain recommended emergency procedures, such as how to handle a spill.
Regulations
The disposal of chemical waste is controlled in all workplaces, including laboratories and manufacturing plants. The majority of chemical wastes is generated in laboratories. However, there are other types not related to laboratories. These include contaminated soils, building materials, paints and lubricants. Expired chemicals must also be disposed of according to regulations.
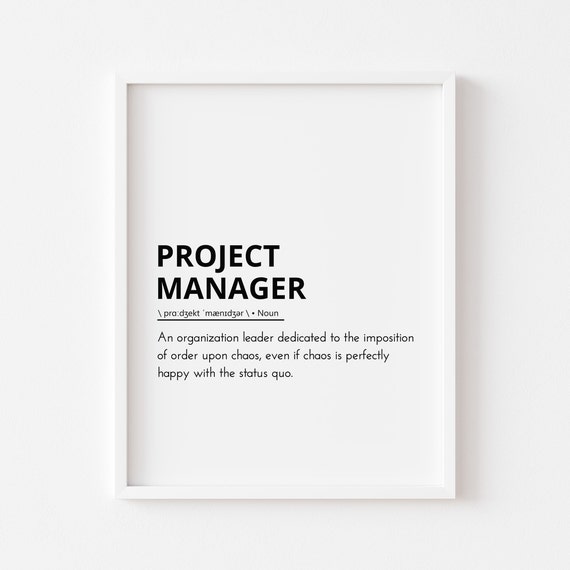
Proper handling of hazardous substances is an integral part safety protocols. It is the responsibility and obligation of employees. This is done so that employees are not exposed and to prevent any potential contamination. Two University programs were created to assist employees in meeting regulations.
Collection
The Chemical Collection Request Form is the first step in the collection procedure. This form must also be completed for each waste container. Multiple containers of the same chemical refuse are often combined into one request. The online form can then be submitted. Once you submit the request online, a CCR number will be assigned and a Dangerous Waste label will be created for your waste containers. Once you have the information, print the label. Then you can transfer it to your trash container's labels.
Chemical waste can be any substance or mixture of chemicals that is no longer used. These materials can be either in solid, liquid, and gaseous forms. To avoid pollution charges, it is crucial to collect chemical waste.
Storage
Proper chemical waste storage is crucial to prevent contamination. This is why it is important to seperate wastes according to hazard. You should store them in compatible containers. For example, chemicals containing hydrofluoric should not stored in metal or glass containers. For liquids-containing wastes, containers should be designed for liquids. Small containers should not be used to store large quantities of liquids.
Containers should be tightly sealed. The closures must be leak-proof. Placing contaminated glassware in a punctureproof container is also a must. Hazardous waste should be clearly marked on the containers.
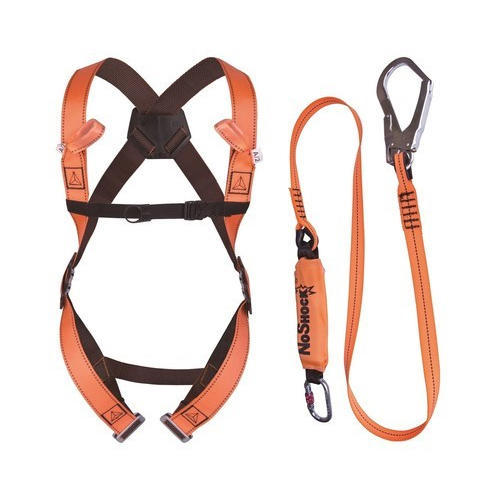
Disposal
It is crucial to understand the proper disposal procedures for hazardous waste produced by your company. The Texas Commission on Environmental Quality (TEQA) regulates hazardous wastes. Incorrect disposal can lead to substantial fines or legal action. The best way to dispose of this type of waste is through a hazardous waste management system.
Chemical waste refers to the disposal of chemicals that are no longer in use. These wastes come in many forms. Some of these wastes are hazardous while others are safe. Chemical waste can be considered hazardous for household use or universal. For a chemical to be considered hazardous, it must demonstrate four characteristics. They can be radioactive, toxic, flammable or biohazardous. For safe disposal, some chemicals should be kept in containers.
FAQ
What are the 4 main functions of management?
Management is responsible of planning, organizing, leading, and controlling people as well as resources. It includes creating policies and procedures, as well setting goals.
Management assists an organization in achieving its goals by providing direction, coordination and control, leadership, motivation, supervision and training, as well as evaluation.
Management has four primary functions:
Planning - Planning refers to deciding what is needed.
Organizing - Organization involves deciding what should be done.
Directing - Directing means getting people to follow instructions.
Controlling - Controlling means ensuring that people carry out tasks according to plan.
How do you manage employees effectively?
Managing employees effectively means ensuring that they are happy and productive.
It means setting clear expectations for them and keeping an eye on their performance.
Managers must be clear about their goals and those of their teams in order to succeed.
They must communicate clearly with their staff. And they need to ensure that they reward good performance and discipline poor performers.
They also need to keep records of their team's activities. These include:
-
What was the result?
-
How much work did you put in?
-
Who did it?
-
How did it get done?
-
Why was this done?
This information can help you monitor your performance and to evaluate your results.
What is TQM and how can it help you?
The industrial revolution saw the realization that prices alone were not sufficient to sustain manufacturing companies. This led to the birth of quality. They needed to improve the quality and efficiency of their products if they were to be competitive.
To address this need for improvement management created Total Quality Management (TQM) which aimed to improve all aspects of an organization's performance. It included continuous improvement and employee involvement as well as customer satisfaction.
Statistics
- The average salary for financial advisors in 2021 is around $60,000 per year, with the top 10% of the profession making more than $111,000 per year. (wgu.edu)
- As of 2020, personal bankers or tellers make an average of $32,620 per year, according to the BLS. (wgu.edu)
- 100% of the courses are offered online, and no campus visits are required — a big time-saver for you. (online.uc.edu)
- Our program is 100% engineered for your success. (online.uc.edu)
- The profession is expected to grow 7% by 2028, a bit faster than the national average. (wgu.edu)
External Links
How To
What is Lean Manufacturing?
Lean Manufacturing methods are used to reduce waste through structured processes. They were developed in Japan by Toyota Motor Corporation (in the 1980s). The aim was to produce better quality products at lower costs. Lean manufacturing emphasizes removing unnecessary steps from the production process. It is composed of five fundamental elements: continuous improvement; pull systems, continuous improvements, just-in–time, kaizen, continuous change, and 5S. Pull systems involve producing only what the customer wants without any extra work. Continuous improvement refers to continuously improving existing processes. Just-in time refers to components and materials being delivered right at the place they are needed. Kaizen refers to continuous improvement. It is achieved through small changes that are made continuously. Finally, 5S stands for sort, set in order, shine, standardize, and sustain. These five elements can be combined to achieve the best possible results.
The Lean Production System
Six key concepts are the basis of lean production:
-
Flow - The focus is on moving information and material as close as possible to customers.
-
Value stream mapping- This allows you to break down each step of a process and create a flowchart detailing the entire process.
-
Five S’s - Sorted, In Order. Shine. Standardize. And Sustain.
-
Kanban - use visual signals such as colored tape, stickers, or other visual cues to keep track of inventory;
-
Theory of constraints: Identify bottlenecks and use lean tools such as kanban boards to eliminate them.
-
Just-in Time - Send components and material directly to the point-of-use;
-
Continuous improvement is making incremental improvements to your process, rather than trying to overhaul it all at once.