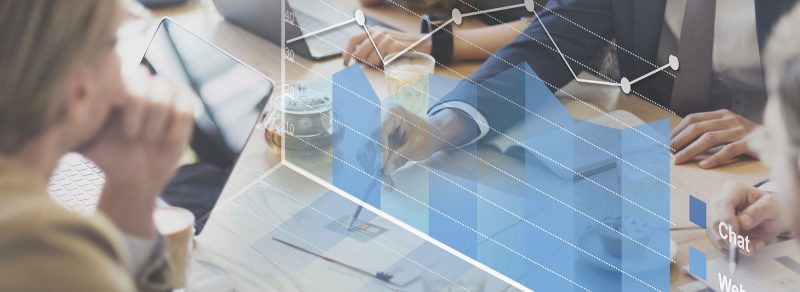
Many studies have been done to examine the dynamic of work flexibility. These studies examined the role of work flexibility in job satisfaction and productivity, as well the impact of flexible work arrangements on organizational performance and productivity. They also looked at the impact of flexible work arrangements on the well-being of employees. They have also examined the benefits to employees and employers.
These studies provide important insight into the effects of flexibility on employee performance. These studies have shown that flexible work arrangements lead to higher job satisfaction, performance, and overall health. They also show greater ability to manage personal and professional life. Researchers also found that flexible employees have higher levels of psychosocial and preventive skills than permanent employees.
This study also examines the effect of flexible working arrangements on employees' wellbeing and performance, with particular attention to the four types of work flexibilities. These are working time flexibility (working space flexibility), working time flexibility, urgent management actions, functional flexibility, and managerial flexibility. This study examines the effects of different types of work flexibility on employee performance using a comparative analysis.
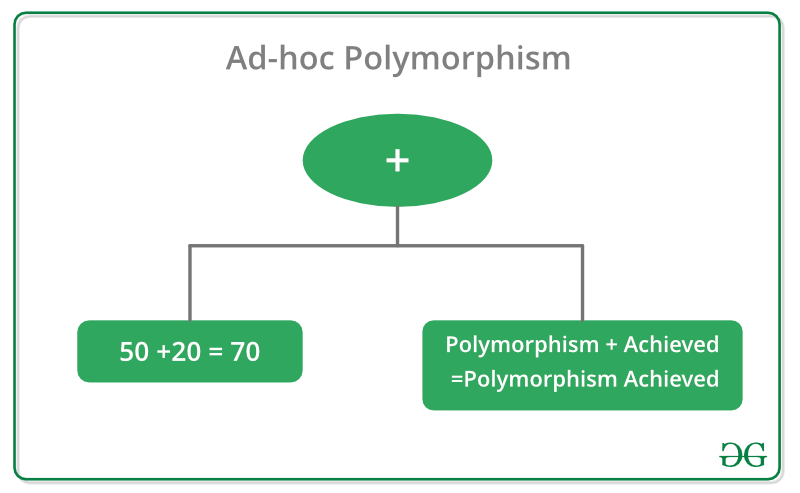
The study also focuses on the impact of flexible working arrangements on the wellbeing, productivity, and organizational performance of employees. The research was based on the viewpoints of Romanian employees. To collect the views of employees, the study used the multiple correspondence analyze (MCA). MCA is a statistical technique that measures the magnitude of the explanation of variance in factorial scores. The MCA method differs to the PCA in that the dependent variable does not need to be observed. The MCA method assumes that the information used to generate composite indicators.
MCA identifies the first dimension as the ordering consistency principle for the factorial scores. The factorial scores on this axis are expected to increase over time. These coefficients are more likely to be significant than the threshold at 10%.
The main findings indicate that working time flexibility, functional flexibility, working space flexibility, and urgent management measures contribute most to the employee flexibility composite indicator. These three items are particularly important for job performance and job satisfaction.
This study examines the effects of various forms of flexibility on employee performance, job satisfaction and organizational performance. The importance of new workplaces in job satisfaction and job performance is highlighted by this study. The study has identified that new workspace types contribute to higher organizational performance and job performance, while increasing employee motivation and satisfaction.
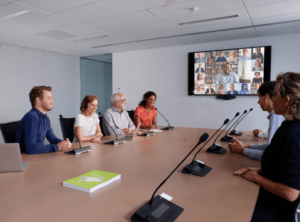
The authors used a comparative analysis to determine a positive correlation between work space flexibility, functional flexibility, and working time flexibility. A binary logistic regression model was used to determine the correlation between these variables. The Hosmer-Lemeshow test has validated this model. This test proves that the model accurately reflects the data.
FAQ
What is the role of a manager in a company?
There are many roles that a manager can play in different industries.
The manager oversees the day-to-day activities of a company.
He/she ensures the company meets its financial commitments and produces goods/services that customers demand.
He/she makes sure that employees adhere to the rules and regulations as well as quality standards.
He/she designs new products or services and manages marketing campaigns.
What kind people use Six Sigma?
People who have worked with statistics and operations research will usually be familiar with the concepts behind six sigma. It can be used by anyone in any business aspect.
This requires a lot of dedication, so only people with great leadership skills can make the effort to implement it.
What are management concepts, you ask?
Management Concepts are the management principles and practices that managers use in managing people and resources. These topics include job descriptions, performance evaluations and training programs. They also cover human resource policies, job description, job descriptions, job descriptions, employee motivation, compensation systems, organizational structures, and many other topics.
Statistics
- 100% of the courses are offered online, and no campus visits are required — a big time-saver for you. (online.uc.edu)
- The average salary for financial advisors in 2021 is around $60,000 per year, with the top 10% of the profession making more than $111,000 per year. (wgu.edu)
- This field is expected to grow about 7% by 2028, a bit faster than the national average for job growth. (wgu.edu)
- The profession is expected to grow 7% by 2028, a bit faster than the national average. (wgu.edu)
- UpCounsel accepts only the top 5 percent of lawyers on its site. (upcounsel.com)
External Links
How To
How is Lean Manufacturing done?
Lean Manufacturing methods are used to reduce waste through structured processes. They were created by Toyota Motor Corporation in Japan in the 1980s. The aim was to produce better quality products at lower costs. Lean manufacturing focuses on eliminating unnecessary steps and activities from the production process. It is made up of five elements: continuous improvement, continuous improvement, just in-time, continuous change, and 5S. Pull systems allow customers to get exactly what they want without having to do extra work. Continuous improvement involves constantly improving upon existing processes. Just-in–time refers when components or materials are delivered immediately to their intended destination. Kaizen is continuous improvement. This can be achieved by making small, incremental changes every day. Fifth, the 5S stand for sort, set up in order to shine, standardize, maintain, and standardize. To achieve the best results, these five elements must be used together.
Lean Production System
Six key concepts are the basis of lean production:
-
Flow - focuses on moving information and materials as close to customers as possible.
-
Value stream mapping - break down each stage of a process into discrete tasks and create a flowchart of the entire process;
-
Five S's - Sort, Set In Order, Shine, Standardize, and Sustain;
-
Kanban - visual cues such as stickers or colored tape can be used to track inventory.
-
Theory of constraints - identify bottlenecks in the process and eliminate them using lean tools like kanban boards;
-
Just-intime - Order components and materials at your location right on the spot.
-
Continuous improvement - make incremental improvements to the process rather than overhauling it all at once.