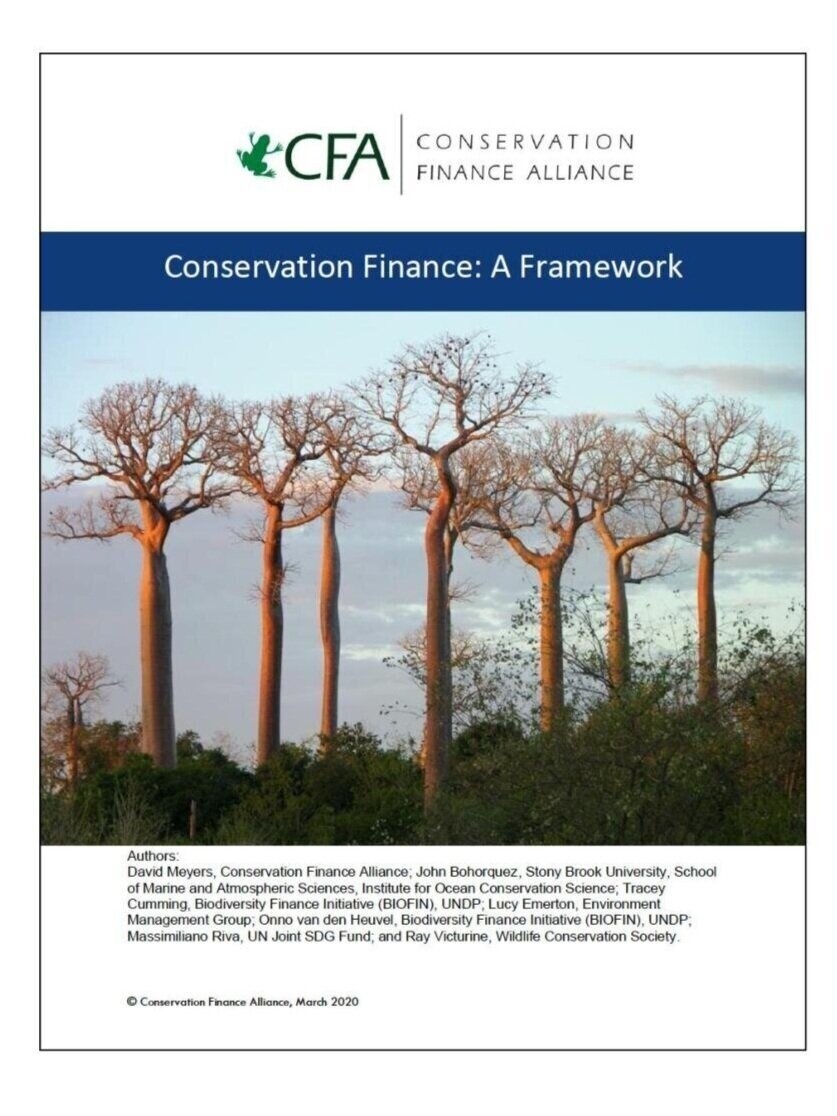
You can use time management strategies to organize your tasks in small steps, prioritize them, and make them easier. Like all strategies, you will need to adjust or modify your plan from time in time. Ultimately, you should always strive to improve your strategies. There will always be a way to overcome any roadblocks.
Pomodoro Technique
Pomodoro Technique: If you have ever wondered how to better manage your time, this may be the right tool for you. Francesco Cirillo, a late 1980s researcher, developed the Pomodoro Technique. This method breaks down work into 25 minute intervals. This breaks down the work into short periods so you can continue working for a long time and then take a brief break.
With the Pomodoro Technique, you can set a timer to tell you when to take a break. This can help you avoid working too hard. It allows you to prioritise tasks and breaks them into manageable segments.
Swiss Cheese Method
Swiss Cheese is a time-management technique that helps you break down big tasks into manageable pieces and gets things done. It works similar to cutting a salami into bite-sized pieces. People who have limited time can start by breaking down large projects in manageable pieces. This helps people to manage their time better.
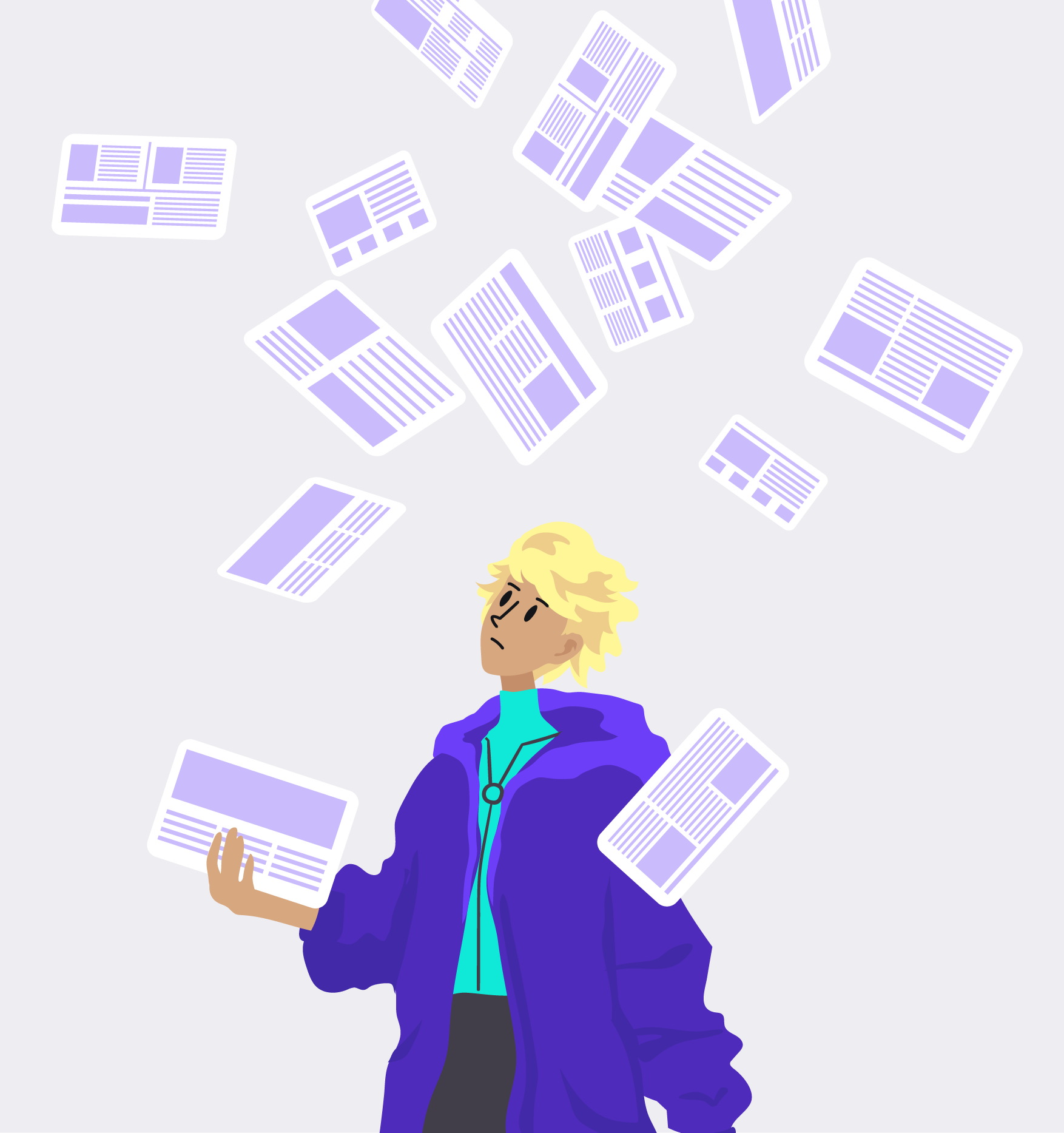
For projects that are difficult to manage, the Swiss Cheese method is a good choice. It breaks down the project into smaller pieces and allows you to plan and map progress. You can also mark small achievements to celebrate along your journey. You can also track the details and tasks completed for the project.
80/20 rule
Prioritizing your tasks based on which will give you the most results is the 80/20 rule for managing time. It doesn't necessarily mean that you should disregard tasks that don't yield as many results. Focus on the ones that are most valuable and produce the highest quality results. You can set high standards and be more energetic when working on projects by following this rule.
It's important to note that the 80/20 rule does not apply in all cases. It is a general principle based on the Pareto Principle. It states that 80 per cent of results are due to 20 percent causes. This rule has been extensively used in marketing and design as well as teaching.
Breaking tasks into smaller steps
The best way to reduce time is to break down large tasks into smaller chunks. You can concentrate on each step and complete large tasks in a manageable way. If you have many tasks to complete, breaking down tasks into smaller steps is a great way to focus and accomplish them in a shorter time. These tasks may be complicated or time-consuming, and a breakup strategy can make them seem much more manageable.
The first step in task breakdown is to clearly define each task. Each step should be clearly defined. Also, determine the time it will take. Once you have identified each step, it is time to put them on your calendar.

Taking regular breaks
Regular breaks are an integral part of your day. It can also help keep you sharp and focused. According to a study, 90 percent of bosses encourage employees to take frequent breaks. 86 percent also agree that breaks increase productivity. Breaks are also a way to relax and reduce stress. Taking breaks can be anything from a 10-minute break to a vacation, depending on what you plan to do during your time off.
It is important that you take breaks on a regular basis. But, it's also important to schedule those breaks. You can even set a time for each break, so that you'll remember when you need one. To maximize your time off, you should aim for breaks that last 20 minutes or less.
FAQ
How does Six Sigma work?
Six Sigma uses statistics to measure problems, find root causes, fix them, and learn from past mistakes.
The first step in solving a problem is to identify it.
The next step is to collect data and analyze it in order to identify trends or patterns.
Then, corrective actions can be taken to resolve the problem.
The data are then reanalyzed to see if the problem is solved.
This cycle continues until there is a solution.
What are the most common errors made by managers?
Managers sometimes make their own job harder than necessary.
They may not delegate enough responsibilities and not provide sufficient support.
A majority of managers lack the communication skills needed to motivate their team and lead them.
Managers can set unrealistic expectations for their employees.
Managers may attempt to solve all problems themselves, rather than delegating it to others.
What are your main management skills
Business owners need to have management skills, no matter how small or large they may be. These skills include the ability manage people, finances and resources as well as other factors.
When you need to manage people, set goals, lead teams, motivate them, solve problems, develop policies and procedures and manage change, management skills are essential.
You can see that there are many managerial duties.
Statistics
- UpCounsel accepts only the top 5 percent of lawyers on its site. (upcounsel.com)
- This field is expected to grow about 7% by 2028, a bit faster than the national average for job growth. (wgu.edu)
- 100% of the courses are offered online, and no campus visits are required — a big time-saver for you. (online.uc.edu)
- Hire the top business lawyers and save up to 60% on legal fees (upcounsel.com)
- The average salary for financial advisors in 2021 is around $60,000 per year, with the top 10% of the profession making more than $111,000 per year. (wgu.edu)
External Links
How To
How can Lean Manufacturing be done?
Lean Manufacturing uses structured methods to reduce waste, increase efficiency and reduce waste. They were developed in Japan by Toyota Motor Corporation (in the 1980s). The main goal was to produce products at lower costs while maintaining quality. Lean manufacturing emphasizes removing unnecessary steps from the production process. It is composed of five fundamental elements: continuous improvement; pull systems, continuous improvements, just-in–time, kaizen, continuous change, and 5S. It is a system that produces only the product the customer requests without additional work. Continuous improvement involves constantly improving upon existing processes. Just-in–time refers when components or materials are delivered immediately to their intended destination. Kaizen means continuous improvement, which is achieved by implementing small changes continuously. Finally, 5S stands for sort, set in order, shine, standardize, and sustain. These five elements work together to produce the best results.
Lean Production System
Six key concepts make up the lean manufacturing system.
-
Flow - focus on moving material and information as close to customers as possible;
-
Value stream mapping: This is a way to break down each stage into separate tasks and create a flowchart for the entire process.
-
Five S's – Sort, Put In Order Shine, Standardize and Sustain
-
Kanban - visual cues such as stickers or colored tape can be used to track inventory.
-
Theory of constraints: Identify bottlenecks and use lean tools such as kanban boards to eliminate them.
-
Just-in Time - Send components and material directly to the point-of-use;
-
Continuous improvement - Make incremental improvements rather than overhauling the entire process.