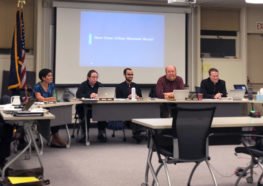
A supply chain decision making framework is a process that will help companies make decisions about different aspects of their business. Communication is a crucial component. The rational process includes five steps: identifying the problem, understanding its potential solutions and gathering data. Next, analyze the possible outcomes. Finally, choose the best solution and put it into practice.
Inventory is an important supply chain driver
Management of inventory is a key function of manufacturing firms. It allows you to supply the right product at a right time. This function is even more critical in a global economic environment, where products are manufactured almost anywhere. It is crucial to a company’s efficiency as well as responsiveness.
Being able to anticipate customer demands and respond to changing situations is critical to inventory management. The data that companies share about their production schedules or inventory levels must be shared with their partners. This allows them to quickly react to market changes. Inventory management is crucial in this dynamic environment to ensure that companies can meet customers' needs.
Collaboration and communication are crucial.
Collaboration and communication are crucial to supply chain decision making in today's fast-paced environment. These relationships allow companies to be more responsive to market changes and to differentiate themselves from their competitors. Collaboration can help companies gain access to new resources, improve their skills, and stay competitive. It can also help businesses grow their customer base.
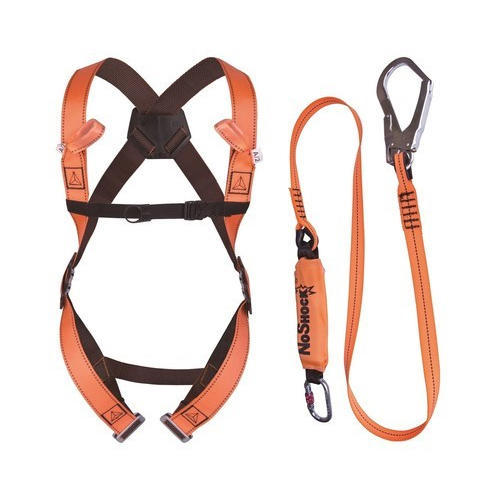
Creating successful collaborative relationships requires high levels of commitment and trust. Organisations must also have a culture that supports collaboration.
Financial attributes
A supply chain decision making framework should be based on financial and environmental attributes, and not just the economic ones. It is crucial to improve cash flow across the supply chain. These attributes will influence the level of working capital at the suppliers, as well as at the buyers. This is because cash flow levels directly correlate with the level of financial leverage, access capital and financial stability of suppliers. Financial attributes are therefore crucial to improve SCF, and they also play an important role in environmental policy and investment in green technologies. Furthermore, financial and environmental policies are directly linked to social values.
The proposed framework provides a decision-making framework for the supply chain, and it interlinks the different components. It also provides open research questions. The framework is applicable across industries and sectors.
It is important to consider the environmental attributes
A growing trend is to incorporate environmental attributes into supply chain decision-making frameworks. This is due to a greater awareness of environmental issues. Companies use environmental performance metrics for a variety purposes, including to identify improvement opportunities and improve co-operation with suppliers. While environmental performance measurement can be a complex issue, it is important to remember that the benefits to both parties can be substantial.
These attributes include social, financial and environmental criteria. This framework is intended to assist businesses in selecting environmentally friendly suppliers. It should also assist them in adopting environmental practices within their companies.
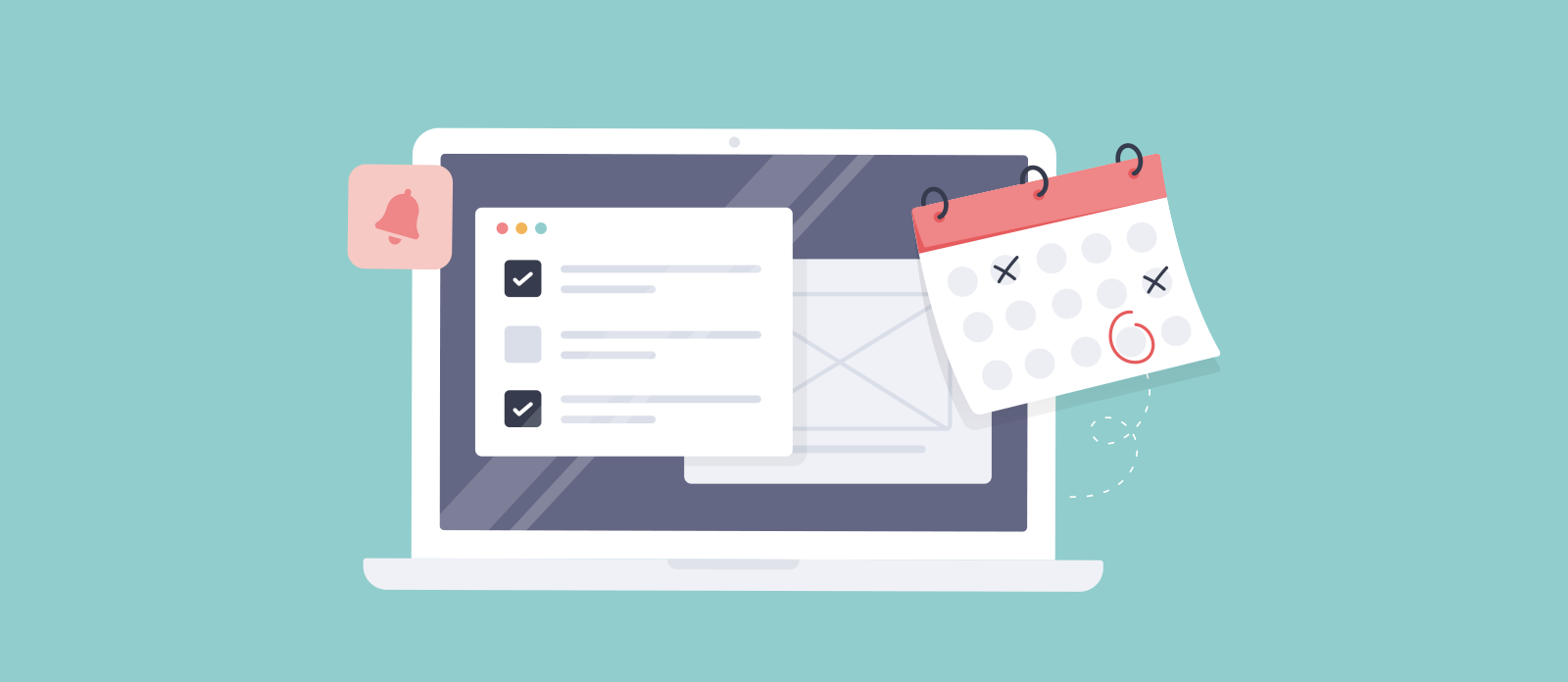
Prioritizing
It is important to prioritize demand in supply chain decisions. It is essential to identify the highest-profitable market and allocate resources accordingly. Sometimes, this may mean delaying orders or offering a substitute product. This will help to manage risk. The entire process should be documented and communicated with all levels of management. While the supply-side should give inputs on costs, the demand sides should have the most detailed information about customer wants and sales objectives.
Next is to identify possible opportunities to obtain capacity, raw material, and labor pools. A company might look at alternative sources for raw materials that offer lower prices and longer lead times. However, it should also be noted that this can erode margin and working capital. Similar, expansions may be required during off-peak hour or to ensure additional transport capacity.
FAQ
Why is it important that companies use project management methods?
Project management techniques ensure that projects run smoothly while meeting deadlines.
This is because many businesses depend heavily upon project work to produce products and services.
Companies must manage these projects effectively and efficiently.
Companies could lose their time, reputation, and money without effective project management.
How can we create a culture of success in our company?
A company culture that values and respects its employees is a successful one.
It is based on three principles:
-
Everybody has something to offer.
-
People are treated fairly
-
Individuals and groups can have mutual respect
These values are reflected by the way people behave. For example, they will treat others with courtesy and consideration.
They will listen respectfully to the opinions of others.
And they will encourage others to share ideas and feelings.
The company culture promotes collaboration and open communication.
People are free to speak out without fear of reprisal.
They are aware that mistakes can be accepted if they are treated honestly.
Finally, the company culture promotes honesty and integrity.
Everyone is aware that truth must be told.
Everyone understands there are rules that they must follow.
People don't expect special treatment or favors.
It seems so difficult sometimes to make sound business decisions.
Complex systems and many moving parts make up businesses. Their leaders must manage multiple priorities, as well as dealing with uncertainty.
To make good decisions, you must understand how these factors affect the entire system.
You must first consider what each piece of the system does and why. It's important to also consider how they interact with each other.
Ask yourself if there are hidden assumptions that have influenced your behavior. You might consider revisiting them if they are not.
For help, ask someone else if you're still stumped after all the above. You may be able to see things from a different perspective than you are and gain insight that can help you find a solution.
Six Sigma is so well-known.
Six Sigma is easy to use and can lead to significant improvements. Six Sigma also gives companies a framework for measuring improvement and helps them focus on what is most important.
What is the difference between TQM and Six Sigma?
The main difference between these two quality management tools is that six sigma focuses on eliminating defects while total quality management (TQM) focuses on improving processes and reducing costs.
Six Sigma is a methodology for continuous improvement. It emphasizes the elimination and improvement of defects using statistical methods, such as control charts, P-charts and Pareto analysis.
This method seeks to decrease variation in product output. This is done by identifying root causes and rectifying them.
Total quality management is the measurement and monitoring of all aspects within an organization. This includes training employees to improve their performance.
It is frequently used as an approach to increasing productivity.
Statistics
- Hire the top business lawyers and save up to 60% on legal fees (upcounsel.com)
- 100% of the courses are offered online, and no campus visits are required — a big time-saver for you. (online.uc.edu)
- The profession is expected to grow 7% by 2028, a bit faster than the national average. (wgu.edu)
- Your choice in Step 5 may very likely be the same or similar to the alternative you placed at the top of your list at the end of Step 4. (umassd.edu)
- The BLS says that financial services jobs like banking are expected to grow 4% by 2030, about as fast as the national average. (wgu.edu)
External Links
How To
How do you do the Kaizen method?
Kaizen means continuous improvement. The term was coined in the 1950s at Toyota Motor Corporation and refers to the Japanese philosophy emphasizing constant improvement through small incremental changes. It is a process where people come together to improve their processes.
Kaizen is one of the most effective methods used in Lean Manufacturing. In this concept, employees who are responsible for the production line must identify problems that exist during the manufacturing process and try to solve them before they become big issues. This improves the quality of products, while reducing the cost.
Kaizen is an approach to making every worker aware and alert to what is happening around them. To prevent problems from happening, any problem should be addressed immediately. If someone is aware of a problem at work, he/she should inform his/her manager immediately.
When doing kaizen, there are some principles we must follow. When working with kaizen, we always start with the end result and move towards the beginning. For example, if we want to improve our factory, we first fix the machines that produce the final product. Next, we fix the machines which produce components. Then, we fix those who work directly with the machines.
This method is known as kaizen because it focuses upon improving every aspect of the process step by step. When we are done fixing the whole factory, we go back to the beginning and continue until we reach perfection.
You need to know how to measure the effectiveness of kaizen within your business. There are several ways that you can tell if your kaizen system is working. One of these ways is to check the number of defects found on the finished products. Another way is to check how much productivity has grown since kaizen was implemented.
Another way to know whether kaizen is working is to ask yourself why did you decide to implement kaizen. It was because of the law, or simply because you wanted to save some money. Did you really believe it would lead to success?
Congratulations! Now you're ready for kaizen.