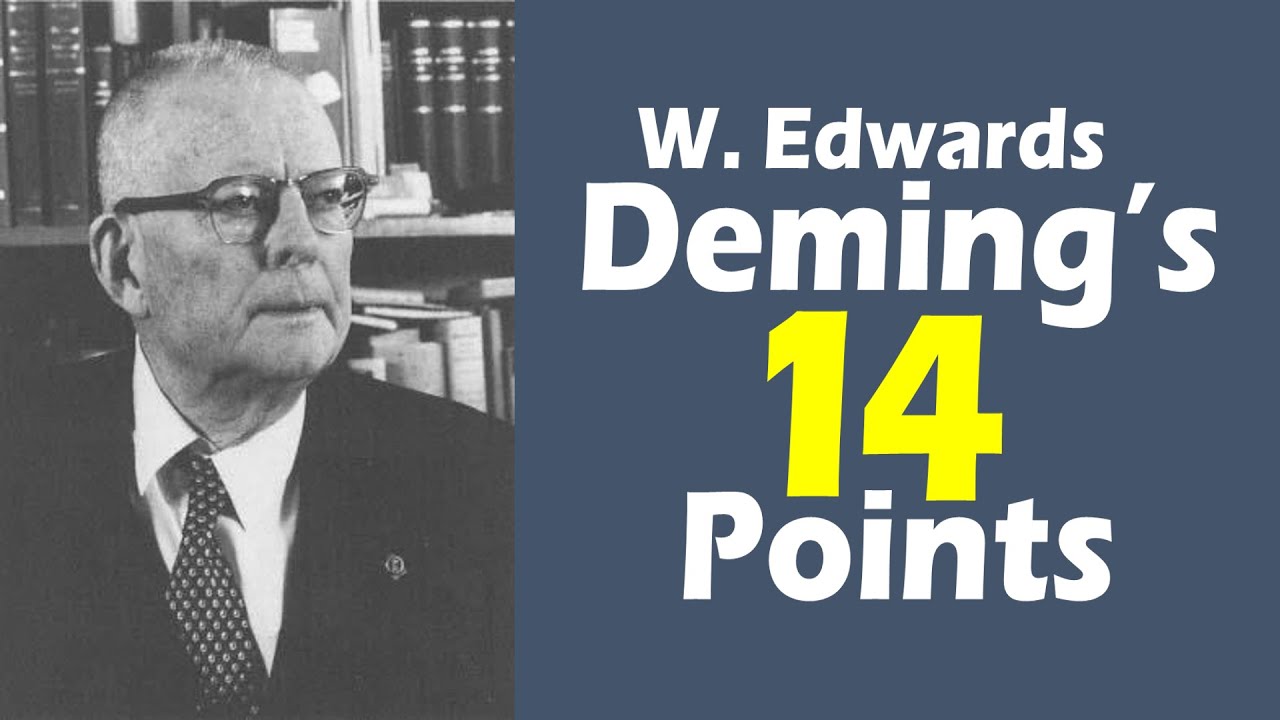
Process safety management is a methodical approach to the maintenance of the integrity and operation of a facility's processes and systems. This system must be up-to-date at least five years after it is established. Process safety management aims to prevent accidents. These steps will help you get started with process management. These steps will make your facility as safe as possible, and prevent accidents.
Process safety management can be described as a disciplined framework that manages the integrity of operating system and process processes.
Process safety management's goal is to decrease the number of incidents. This will increase sustained value and productivity. It is about controlling the risks in the plant and making equipment safer. It requires strict adherence and assessment of hazards. It includes the training and maintenance of your plant, as well as process control. It is an essential element of a safety-conscious business.
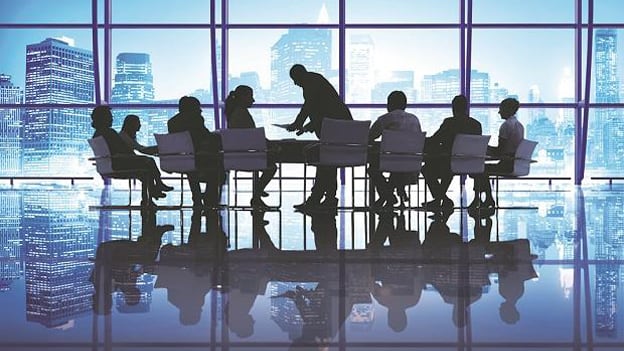
It should be up-to-date every five years
The Occupational Safety and Health Administration (OSHA) requires that processes be reviewed and updated regularly. This includes the development and updating of safety procedures and processes. All employees involved in the process must have access. For five years, written procedures and reports must be retained. Employees must always have access to the most current process safety information. To meet these requirements, employers can hire safety risk management specialists.
It is a legal requirement in order to operate major hazard facilities
For all major hazard areas, the process safety management system must be implemented. Employers must also develop and implement the program. The plan must include a safety alarm which will notify employees to evacuate. Employees who are physically unable or unwilling to evacuate the hazardous area should be included in this plan.
It helps prevent accidents
A well-designed process management system for safety can enhance a company's safety performance and profitability. It can also help improve the company’s environmental responsibility. It also reduces the chance of accidents. These are all vital areas to ensure the company's long-term success. Below is a brief overview of the various benefits of a process safety management system. It is a system that helps companies prevent and reduce accidents, as well as improve the safety and health of employees and customers.
It can be time-consuming.
A complex and time-consuming task can be involved in process safety management within a hazardous chemical facility. OSHA does not regulate process safety management programs. However, OSHA requires facilities to create a plan and meet 14 minimum requirements. Some companies rely on spreadsheets and forms to collect data and compile risk assessments and other information. This is time-consuming and there is the possibility of human error.
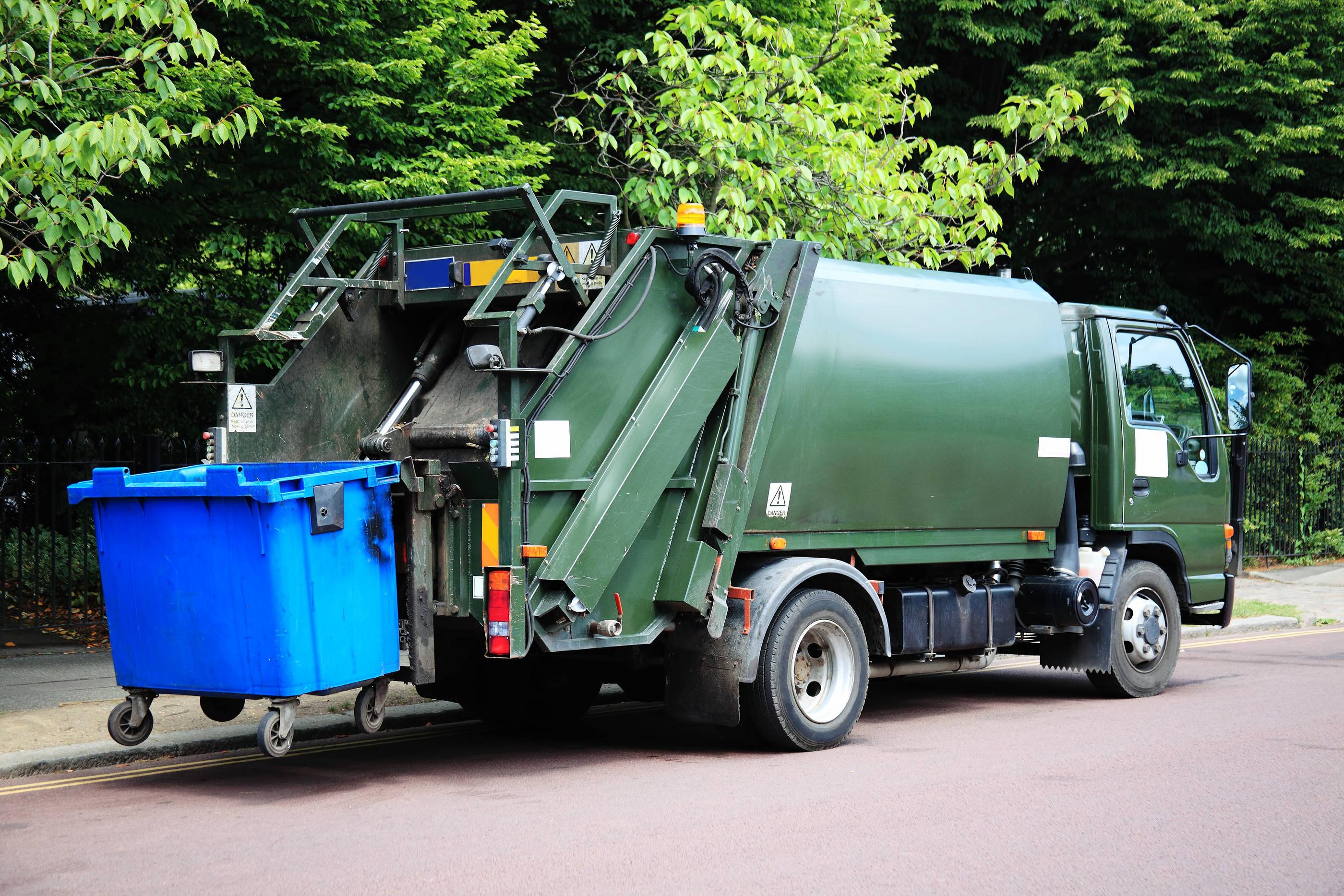
Participation by employees is necessary
Pennsylvania State University adopted a PSM Program that included an Employee Participation element. This element draws upon employees' expertise, knowledge, as well as unique perspectives to enhance safety. This program details the different methods of employee participation and sets minimum requirements. It is important to include all employees in the process safety management process and involve them in all aspects. Employee participation in PSM is essential to avoiding serious incidents. How do you ensure employees are fully engaged in the PSM program?
FAQ
How do you effectively manage employees?
Effectively managing employees requires that you ensure their happiness and productivity.
This includes setting clear expectations for their behavior and tracking their performance.
Managers need clear goals to be able to accomplish this.
They need to communicate clearly and openly with staff members. They also need to make sure that they discipline and reward the best performers.
They also need to keep records of their team's activities. These include:
-
What did you accomplish?
-
How much work did you put in?
-
Who did it all?
-
What was the moment it was completed?
-
Why it was done?
This data can be used to evaluate and monitor performance.
What is the difference between leadership and management?
Leadership is about influencing others. Management is about controlling others.
A leader inspires followers while a manager directs workers.
A leader motivates people and keeps them on task.
A leader develops people; a manager manages people.
Why is project management so important?
Project management techniques ensure that projects run smoothly while meeting deadlines.
Because most businesses depend heavily on project work to produce goods or services,
These projects require companies to be efficient and effective managers.
Companies can lose time, money, and reputation if they don't have a good project management system.
What are management principles?
Management Concepts are the management principles and practices that managers use in managing people and resources. They include such topics as human resource policies, job descriptions, performance evaluations, training programs, employee motivation, compensation systems, organizational structure, and many others.
What are some common mistakes managers make when managing people?
Managers can make their jobs more difficult than necessary.
They may not assign enough responsibilities to staff members and provide them with inadequate support.
Managers often lack the communication skills necessary to motivate and guide their teams.
Managers sometimes set unrealistic expectations of their teams.
Managers might try to solve every problem by themselves rather than delegating the responsibility.
What's the difference between a program and a project?
A program is permanent, whereas a project is temporary.
A project has usually a specified goal and a time limit.
It is often done in a team that reports to another.
A program typically has a set goal and objective.
It is usually implemented by a single person.
What is TQM exactly?
The industrial revolution led to the birth and growth of the quality movement. Manufacturing companies realized they couldn't compete solely on price. They needed to improve the quality and efficiency of their products if they were to be competitive.
To address this need for improvement management created Total Quality Management (TQM) which aimed to improve all aspects of an organization's performance. It included continuous improvement processes, employee involvement, and customer satisfaction.
Statistics
- Our program is 100% engineered for your success. (online.uc.edu)
- Your choice in Step 5 may very likely be the same or similar to the alternative you placed at the top of your list at the end of Step 4. (umassd.edu)
- UpCounsel accepts only the top 5 percent of lawyers on its site. (upcounsel.com)
- 100% of the courses are offered online, and no campus visits are required — a big time-saver for you. (online.uc.edu)
- The BLS says that financial services jobs like banking are expected to grow 4% by 2030, about as fast as the national average. (wgu.edu)
External Links
How To
How do I get my Six Sigma license?
Six Sigma is a quality management tool to improve processes and increase efficiency. It is a method that enables companies to achieve consistent results with their operations. The name derives its meaning from the "sigmas" Greek word, which is composed of two letters that mean six. Motorola invented this process in 1986. Motorola realized that it was important to standardize manufacturing processes so they could produce products quicker and cheaper. There were many people doing the work and they had difficulty achieving consistency. To solve this problem, they decided to use statistical tools such as control charts and Pareto analysis. They would then apply these techniques to all aspects of their operation. After applying the technique, they could make improvements wherever there was potential. When you are trying to obtain your Six Sigma certification, there are three steps. To determine whether you are qualified, the first step is to verify your eligibility. You will need to complete some classes before you can start taking the tests. Once you've passed those classes, you'll start taking the tests. The class material will be reviewed. After that, you can take the test. If you pass, then you will become certified. And finally, you'll be able to add your certifications to your resume.