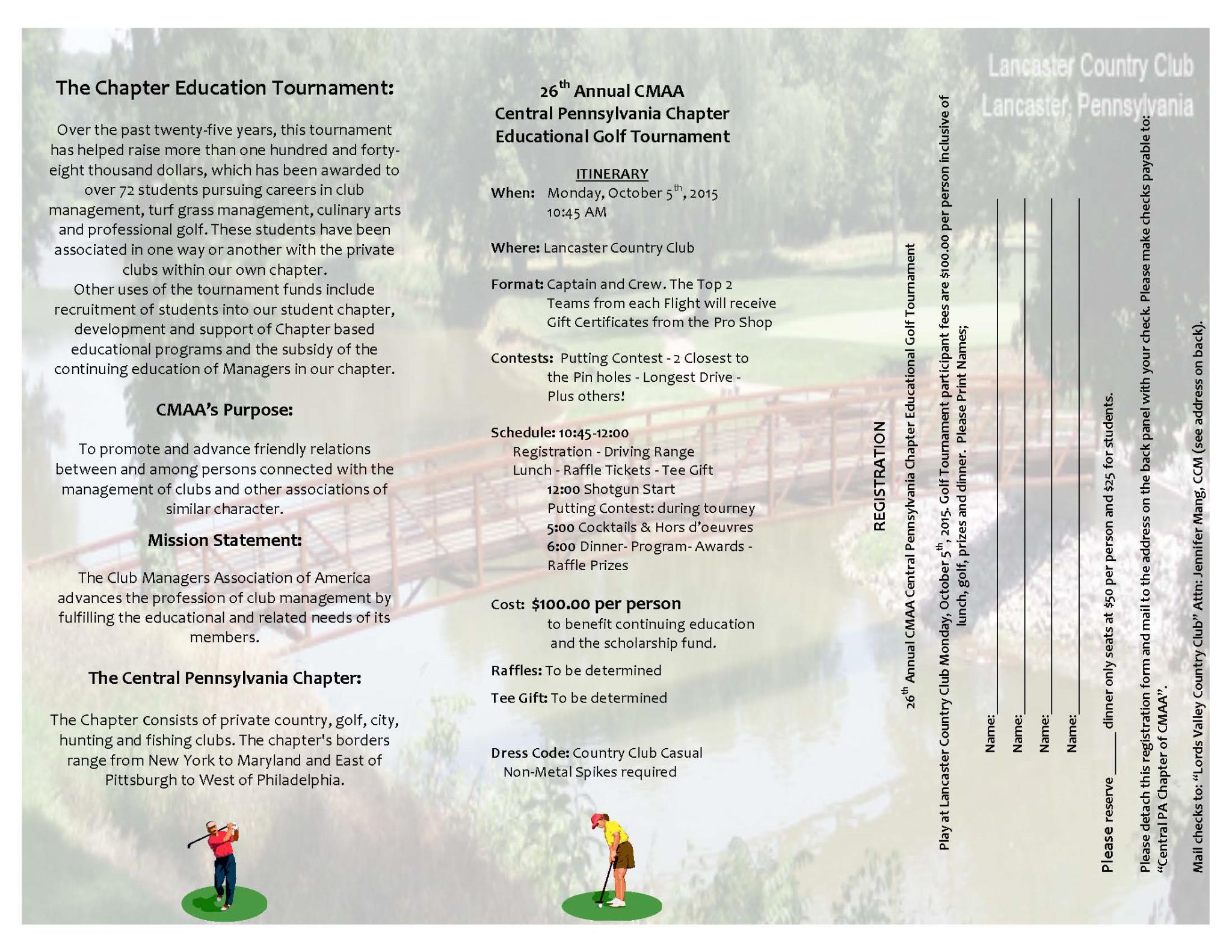
Whether you're in the business of making big bucks or small, you're bound to want to know how to plan and implement a communication strategy that works. Effectively managing a communication strategy is an art in and of itself. It is important that you have a communication plan ready to go when you start a new project or redesign. A solid communication strategy will help your business grow without any risk.
You should also consider how you will manage your communications budget. It is important to choose a budget that allows you to capitalize on opportunities, avoid pitfalls, and meets your financial obligations. You should choose a budget that is sufficient to allow your business to grow without compromising your financial health.
It takes the right mix in media, tactics, time and effort to create a communication plan. The key to a good communication plan is to understand your target audience and identify areas where you can improve upon what you already do. The right people and tools are essential to ensure smooth information flow and proper management. It's important to monitor the effectiveness of your communication strategies and make adjustments if necessary.
A discussion with key stakeholders is the best way of determining what works well. Consult a consultant to help you decide which communication tools work best for your team. Ask your employees what communication tools they use and why. Then, make sure to incorporate their ideas into your communications plan. A communication plan should be based on best practice in order to avoid any major errors.
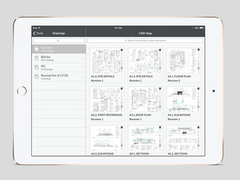
A well-planned and tested communication program is the best. You might want to include your top communication priorities in the budget to help you decide where you should focus your efforts. As I mentioned, it is a smart idea also to consider the cost of implementing the actions you want to take to maximize your dollars. It's a good idea to set up a communications budget that is flexible as your business grows.
FAQ
What are the four main functions of management?
Management is responsible for planning, organizing, directing, and controlling people and resources. Management also involves setting goals and developing policies.
Management is the ability to direct, coordinate, control, motivate, supervise, train, and evaluate an organization's efforts towards achieving its goals.
Management's four main functions are:
Planning - Planning refers to deciding what is needed.
Organizing - Organizing involves deciding how things should be done.
Directing - Directing means getting people to follow instructions.
Controlling – This refers to ensuring that tasks are carried out according to plan.
Six Sigma is so beloved.
Six Sigma can be implemented quickly and produce impressive results. It provides a framework that allows for improvement and helps companies concentrate on what really matters.
How do you define Six Sigma?
People who have worked with statistics and operations research will usually be familiar with the concepts behind six sigma. But anyone can benefit from it.
It requires high levels of commitment and leadership skills to be successful.
What is Kaizen and how can it help you?
Kaizen is a Japanese term which means "continuous improvement." This philosophy encourages employees to continually look for ways to improve the work environment.
Kaizen is built on the belief that everyone should be able do their jobs well.
What are management theories?
Management Concepts are the management principles and practices that managers use in managing people and resources. They include such topics as human resource policies, job descriptions, performance evaluations, training programs, employee motivation, compensation systems, organizational structure, and many others.
Statistics
- UpCounsel accepts only the top 5 percent of lawyers on its site. (upcounsel.com)
- 100% of the courses are offered online, and no campus visits are required — a big time-saver for you. (online.uc.edu)
- The BLS says that financial services jobs like banking are expected to grow 4% by 2030, about as fast as the national average. (wgu.edu)
- Hire the top business lawyers and save up to 60% on legal fees (upcounsel.com)
- Your choice in Step 5 may very likely be the same or similar to the alternative you placed at the top of your list at the end of Step 4. (umassd.edu)
External Links
How To
What is Lean Manufacturing?
Lean Manufacturing techniques are used to reduce waste while increasing efficiency by using structured methods. They were created in Japan by Toyota Motor Corporation during the 1980s. The main goal was to produce products at lower costs while maintaining quality. Lean manufacturing seeks to eliminate unnecessary steps and activities in the production process. It is composed of five fundamental elements: continuous improvement; pull systems, continuous improvements, just-in–time, kaizen, continuous change, and 5S. Pull systems involve producing only what the customer wants without any extra work. Continuous improvement refers to continuously improving existing processes. Just-in time refers to components and materials being delivered right at the place they are needed. Kaizen means continuous improvement, which is achieved by implementing small changes continuously. The 5S acronym stands for sort in order, shine standardize and maintain. These five elements are used together to ensure the best possible results.
Lean Production System
Six key concepts underlie the lean production system.
-
Flow: The goal is to move material and information as close as possible from customers.
-
Value stream mapping - Break down each stage in a process into distinct tasks and create an overview of the whole process.
-
Five S’s - Sorted, In Order. Shine. Standardize. And Sustain.
-
Kanban - use visual signals such as colored tape, stickers, or other visual cues to keep track of inventory;
-
Theory of constraints - identify bottlenecks in the process and eliminate them using lean tools like kanban boards;
-
Just-intime - Order components and materials at your location right on the spot.
-
Continuous improvement is making incremental improvements to your process, rather than trying to overhaul it all at once.