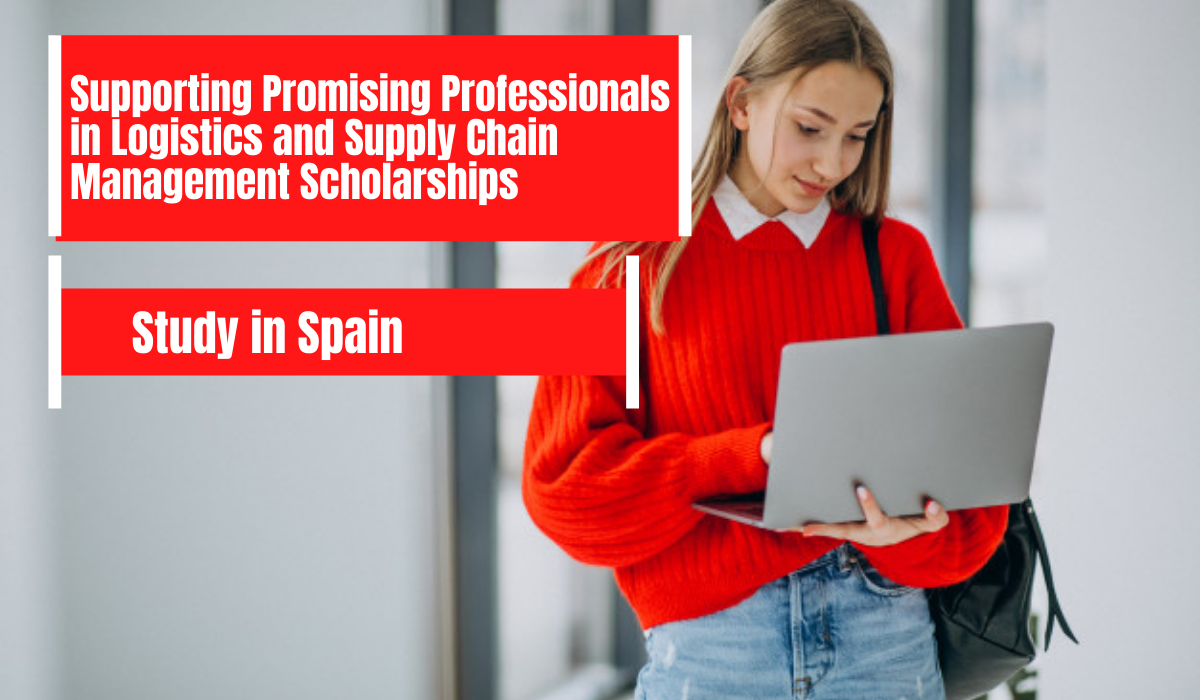
The history of waste management is long. Open-backed carts powered by horses were the first collection vehicles. Motorised versions were introduced during the early 20th century. Closed-top pickup trucks were introduced later. These helped reduce odours, and made it easier to dispose of refuse. The first truck with a hydraulic compactor was the Garwood Load Packer truck in the 1920s. This technology allowed the truck's ability to haul more rubbish per trip. Later, waste-to-energy was developed and the modern bin lorries were born. In the twenty-first century, recycling was also introduced.
Incinerators
Incineration is a waste management process that makes energy by burning waste materials. The heat created by the burning of waste materials is used to generate steam. This steam can be used in order to power a turbine which produces electricity. A typical incineration plant produces approximately two-thirds of an hour of electricity per tonne. This process can also generate district heating. A single plant could burn 600 tonnes of waste per hour and produce around one ton of asphalt per day.
Nottingham, in England, was home to the first incinerator. It was constructed in 1874. Incinerators were added throughout the country over time. Many large cities had destructors. The electricity produced from burning rubbish powered the sewer pumps and electric refuse collection trucks.
Dust-yards
The first example in municipal solid waste management was the dust-yard' system. This innovative system was established in London in the 19th century. This innovative system was based on household waste (coal ash from domestic fires) and its monetary value. This material was sought after by industries including the brick and agricultural industries. The high market value of this material encouraged dust-contractors and other businesses to collect 100% of their residual waste. This helped to ease the transition from municipal solid waste services to public ones in England.
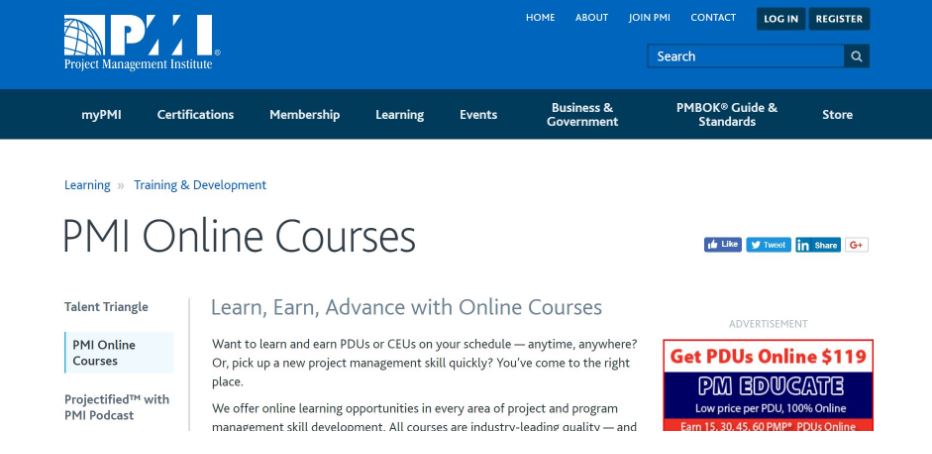
Around 1850 saw the birth of the first waste collection system. A dust-yard was also known as an ash pit, and it was where most people disposed of their trash. This waste was collected by a crew consisting of two men. One man was called a filler and he shoveled the waste into a container from the dust-pit. The other man, who is known as a transporter, carried the basket onto a cart. The process was repeated until full. The cart was then taken to the dust yard, through a chute and dropped on the dust pile.
Inflated reserves
Factors that could increase the cost for environmental services include inflation and labor costs. Companies should report the depreciation cost in their financial statements to avoid such high costs. This can lead to over-inflation of balance sheets for waste management companies. Additionally, companies should keep track of the cost of abandoned and unsuccessful landfill development projects.
In 1997, Waste Management's CEO noticed some irregularities and requested a full review of its accounts. The investigation revealed that $1.7B had been misrepresented by the company's financial statements. The scandal caused the stock price to fall by around a third.
Accounting fraud
This past year, a massive accounting fraud at Waste Management was uncovered by the Securities and Exchange Commission. According to the SEC former Waste Management executives falsified information about their company's financial performance. They also inflated profits by as much as $1.7 billion. In the end, the company was forced by the SEC to settle a class-action lawsuit and pay $7,000,000 in civil fines.
Waste Management used accounting practices which were against generally accepted accounting guidelines to cover up their fraud. They used a variety of accounting techniques to hide expenses such as deferring, erasing and concealing expenses. Waste Management's main fixed assets were garbage trucks and containers. This meant that the depreciation cost for these assets was high and easy to manipulate.
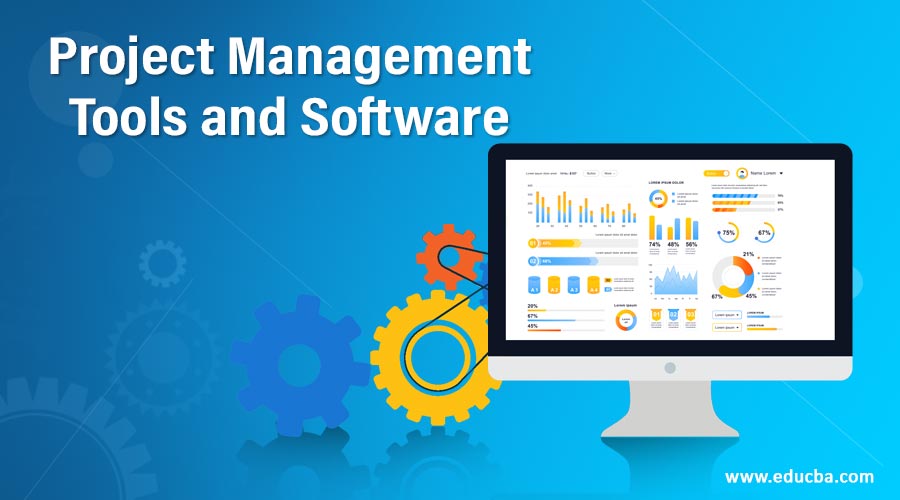
Harvest Power
Harvest Power's innovative business model diverts organic waste from landfills, and converts it into multiple value streams. This reduces net greenhousegas emissions, lowers total disposing costs, and slows down the use of landfill space. It also makes use of agricultural inputs to generate renewable energy. Harvest Power works with this system in order to preserve landfill space and promote the use of renewable energy.
Harvest Power is a proven success in Spain as well as Germany. Its investors believe that the model can also be applied to the United States. It raised $110M in funding in 2012 from Al Gore’s Generation Investment Management and Kleiner Perkins. Waste Management, the nation's largest trash processor, is another investor. It has committed to eliminating all landfills.
FAQ
What are the main management skills?
No matter if they are running a local business or an international one, management skills are vital. These include the ability and willingness to manage people, finances as well resources, time and space.
You will need management skills to set goals and objectives, plan strategies, motivate employees, resolve problems, create policies and procedures, and manage change.
You can see that there are many managerial duties.
What is the difference in a project and program?
A program is permanent, whereas a project is temporary.
A project usually has a specific goal and deadline.
It is often carried out by a team of people who report back to someone else.
A program is usually defined by a set or goals.
It is usually implemented by a single person.
What kind of people use Six Sigma
Six-sigma will be well-known to anyone who has worked in operations research or statistics. It can be used by anyone in any business aspect.
It requires high levels of commitment and leadership skills to be successful.
What are the main four functions of management
Management is responsible to plan, organize, direct, and control people and resources. Management also involves setting goals and developing policies.
Management assists an organization in achieving its goals by providing direction, coordination and control, leadership, motivation, supervision and training, as well as evaluation.
Management's four main functions are:
Planning - Planning is about determining what must be done.
Organizing - Organization involves deciding what should be done.
Directing - Directing means getting people to follow instructions.
Controlling - This is the ability to control people and ensure that they do their jobs according to plan.
Statistics
- This field is expected to grow about 7% by 2028, a bit faster than the national average for job growth. (wgu.edu)
- 100% of the courses are offered online, and no campus visits are required — a big time-saver for you. (online.uc.edu)
- The average salary for financial advisors in 2021 is around $60,000 per year, with the top 10% of the profession making more than $111,000 per year. (wgu.edu)
- UpCounsel accepts only the top 5 percent of lawyers on its site. (upcounsel.com)
- The profession is expected to grow 7% by 2028, a bit faster than the national average. (wgu.edu)
External Links
How To
How do I do the Kaizen Method?
Kaizen means continuous improvement. The Japanese philosophy emphasizes small, incremental improvements to achieve continuous improvement. This term was created by Toyota Motor Corporation in 1950. It's where people work together in order to improve their processes constantly.
Kaizen is one of the most effective methods used in Lean Manufacturing. In this concept, employees who are responsible for the production line must identify problems that exist during the manufacturing process and try to solve them before they become big issues. This improves the quality of products, while reducing the cost.
Kaizen is an approach to making every worker aware and alert to what is happening around them. So that there is no problem, you should immediately correct it if something goes wrong. Report any problem you see at work to your manager.
Kaizen follows a set of principles. The end product is always our starting point and we work toward the beginning. For example, if we want to improve our factory, we first fix the machines that produce the final product. We then fix the machines producing components, and the machines producing raw materials. We then fix the workers that work with those machines.
This method is known as kaizen because it focuses upon improving every aspect of the process step by step. Once the factory is fixed, we return to the original site and work our way back until we get there.
You need to know how to measure the effectiveness of kaizen within your business. There are many ways you can determine if kaizen has been implemented well. One way is to examine the amount of defects on the final products. Another method is to determine how much productivity has improved since the implementation of kaizen.
If you want to find out if your kaizen is actually working, ask yourself why. Is it because the law required it or because you want to save money. Did you really believe that it would be a success factor?
Congratulations if you answered "yes" to any of the questions. You are ready to start kaizen.