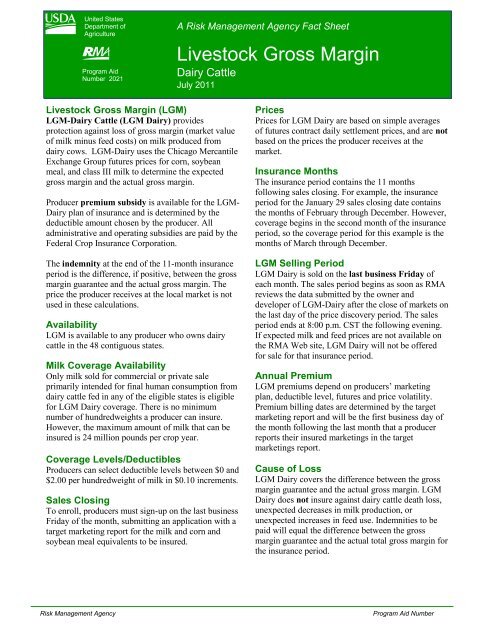
A business flow measurement does not take into account the inherent directionality, or even directionality, of supply networks. Supply networks are complex and have many dependencies. These dependencies can often be interrelated. Additionally, a business flow measurement does not accurately capture the directionality of information flows within networks. Developing a digital supply network requires understanding and considering these issues.
Sustainability
Sustainability of supply networks is a critical element of the supply chain management strategy of multinational corporations. Many companies have made sustainability an important priority and committed themselves to using sustainable suppliers. There are serious risks for businesses if lower-ranking suppliers do not comply with sustainability standards. To combat this problem, the authors looked at three MNC supply networks and discovered several best practices companies can follow. These include setting longterm sustainability goals, and including lower-tier vendors in the sustainability plan.
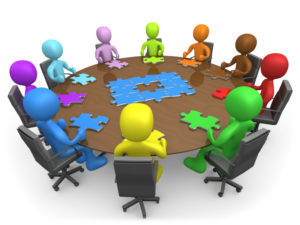
Companies need to set targets and measure progress to demonstrate how they are improving their supply chains. They should also be engaging all stakeholders, including internal staff and consumers. It is important to demonstrate the benefits of sustainable supply chains and to implement proper governance and organizational structures in order to make sustainability efforts a success.
Vertical disintegration in supply chains
Vertical disintegration of supply chains can have a number of consequences for firms. Apart from the potential for greater costs and losses, it can also lead to changes in organisational structures and hierarchies. To improve their overall competitiveness, some companies might choose to decrease their involvement in upstream and downstream activities. However, this is not always a good idea and should only be done in exceptional circumstances.
Vertical integration's main drawback is its limitation of flexibility. This is because it forces it to follow trends within a particular segment. If a competitor has adopted a technology, it might be difficult for a retailer adopt it. If this was the case, the parent would have to invest money in the new technology to keep pace with the competition. Integration can also be complicated due to rapid technological changes. Companies face many challenges in integrating technologies from different parts their supply chains. This can lead to costly problems.
Performance implications of digital supply networks
There are many benefits to digital supply chains, such as increased efficiency, resilience, cost savings and cost savings. However, digital supply chains can increase cybersecurity risks. However, there are several approaches companies can use to mitigate these risks. Let's take a look at some of them. These methods involve data analytics. This technology gives businesses insight into customer preferences and allows them to improve their products. Companies can also use shared data from different sources to predict possible problems and make better, informed decisions.
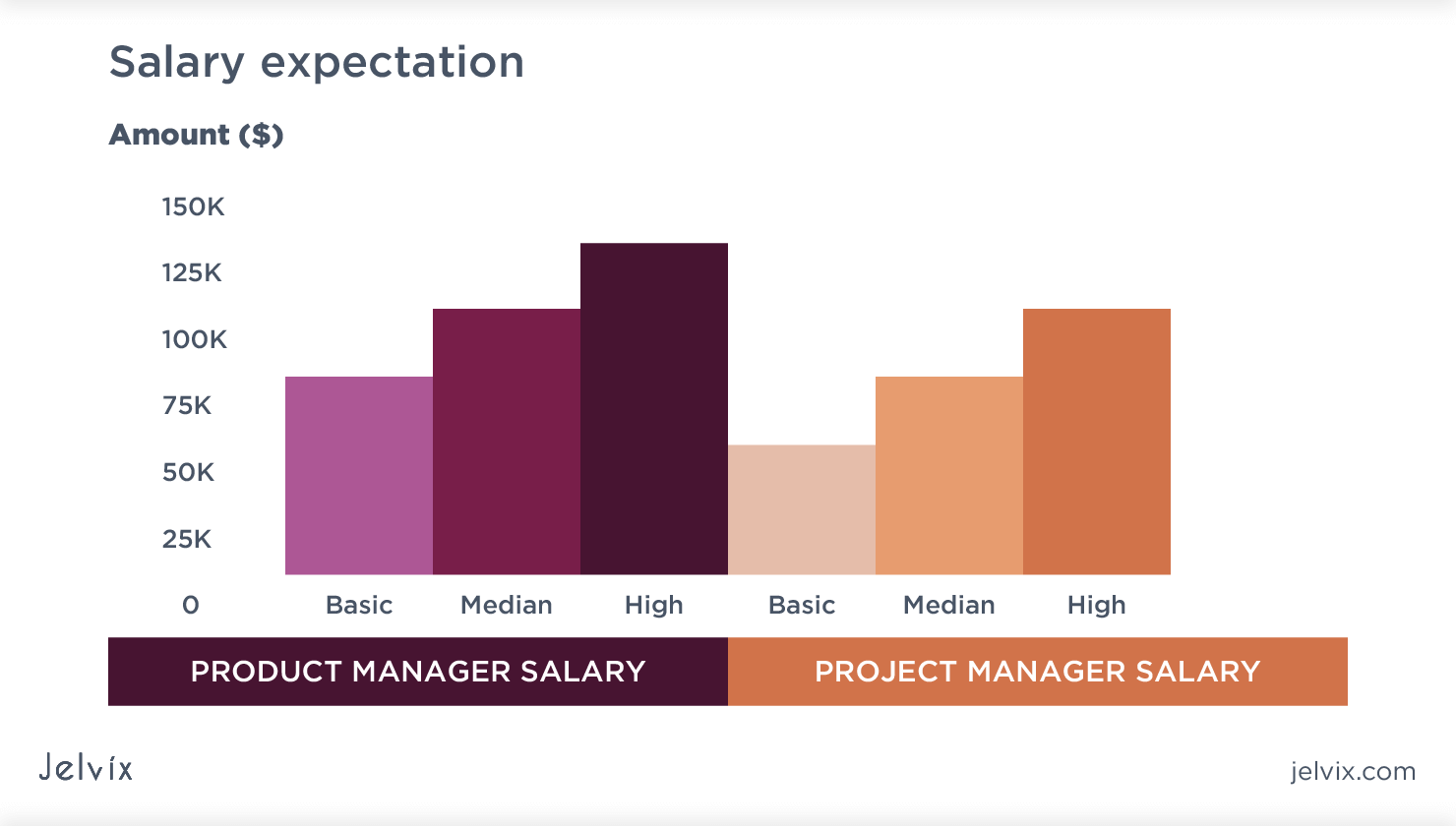
Assessing your supply chain is the first step towards digitalization. This will help you identify and mitigate any risks or issues, as well any potential complications. This will allow you to create an action plan that minimizes any potential dangers. It is important to collaborate with your partners when you have a clear vision of the goals you wish to achieve through the network's digital supply. You can collaborate with your partners to ensure that the digital supply network meets all stakeholders' needs.
FAQ
What's the difference between Six Sigma and TQM?
The main difference between these two quality management tools is that six sigma focuses on eliminating defects while total quality management (TQM) focuses on improving processes and reducing costs.
Six Sigma is a methodology for continuous improvement. This method emphasizes eliminating defects using statistical methods such p-charts, control charts, and Pareto analysis.
This method aims to reduce variation in product production. This is accomplished by identifying the root cause of problems and fixing them.
Total quality management is the measurement and monitoring of all aspects within an organization. It also involves training employees to improve performance.
It is often used to increase productivity.
How can a manager motivate his/her staff?
Motivation is the desire for success.
Enjoyable activities can motivate you.
Another way to get motivated is to see yourself as a contributor to the success of the company.
For example: If you want to be a doctor, you might find it more motivating seeing patients than reading medical books all day.
Another source of motivation is within.
For example, you might have a strong sense of responsibility to help others.
You might even enjoy the work.
If you feel unmotivated, ask yourself why.
Then think about how you can make your life more motivating.
What are the steps in the decision-making process in management?
Managers face complex and multifaceted decision-making challenges. It involves many factors, including but not limited to analysis, strategy, planning, implementation, measurement, evaluation, feedback, etc.
Management of people requires that you remember that they are just as human as you are, and can make mistakes. As such, there is always room for improvement, especially if you're willing to put forth the effort to improve yourself first.
This video will explain how decision-making works in Management. We'll discuss the different types and reasons they are important. Managers should also know how to navigate them. These topics are covered in this course:
Statistics
- The BLS says that financial services jobs like banking are expected to grow 4% by 2030, about as fast as the national average. (wgu.edu)
- The average salary for financial advisors in 2021 is around $60,000 per year, with the top 10% of the profession making more than $111,000 per year. (wgu.edu)
- Our program is 100% engineered for your success. (online.uc.edu)
- The profession is expected to grow 7% by 2028, a bit faster than the national average. (wgu.edu)
- As of 2020, personal bankers or tellers make an average of $32,620 per year, according to the BLS. (wgu.edu)
External Links
How To
How can you implement the Kaizen technique?
Kaizen means continuous improvement. This Japanese term refers to the Japanese philosophy of continuous improvement that emphasizes incremental improvements and constant improvement. It's a team effort to continuously improve processes.
Kaizen is one of the most effective methods used in Lean Manufacturing. In this concept, employees who are responsible for the production line must identify problems that exist during the manufacturing process and try to solve them before they become big issues. This is how you can improve the quality and lower the cost.
Kaizen is about making everyone aware of the world around them. To prevent problems from happening, any problem should be addressed immediately. Report any problem you see at work to your manager.
Kaizen is based on a few principles. The end product is always our starting point and we work toward the beginning. For example, if we want to improve our factory, we first fix the machines that produce the final product. Then, we fix the machines that produce components and then the ones that produce raw materials. Then we fix the workers, who directly work with these machines.
This method, called 'kaizen', focuses on improving each and every step of the process. When we are done fixing the whole factory, we go back to the beginning and continue until we reach perfection.
How to measure kaizen's effectiveness in your business is essential to implement it. There are many ways to tell if kaizen is effective. Another way to determine if kaizen is working well is to look at the quality of the products. Another way to find out how productive your company has been since you implemented kaizen is to measure the increase in productivity.
Another way to know whether kaizen is working is to ask yourself why did you decide to implement kaizen. Did you do it because it was legal or to save money? It was a way to save money or help you succeed.
Congratulations! You are ready to start kaizen.