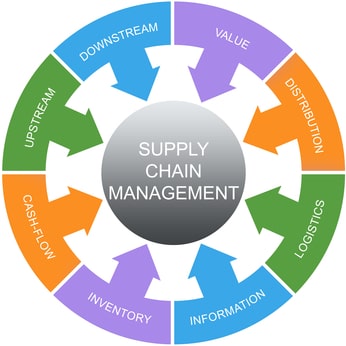
The lack of transparency is a common failure in managing risks. This was highlighted by the scandal over coronavirus fatalities. The siloed, and often insufficient data, are two other problems. The process was not built with risk in view. Risk managers settle for easy access data and fail to recognize risks that could have serious consequences. This is a common issue that is difficult to solve, but it should be avoided.
Negative risks
There are five basic risk response strategies that managers can use to handle negative risks and threats. These strategies are dependent on the type and level of risk. They are dependent on the probability of occurrence as well as the impact that the risk will have. These strategies, which are the most effective, are used when risk is considered critical. When the risk is less critical, the transfer and accept strategy can be used.
People, technology, resources, and processes are affected by both positive and negative risk. If managed properly, even positive risks can produce positive results. A positive risk could result in a project being completed earlier than expected, or a higher return on investment. Negative risks can occur in any situation, and a negative risk may be avoided by implementing the right risk management practices. These risks pose problems and can cause delays and impact on project schedules, budgets, and schedules.
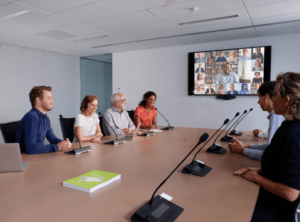
Communication
Risk management is all about communicating risks. Communication must be honest and open, no matter whether it is via a formal document. The risk of misunderstanding the risk exists, but communication professionals can minimize that risk by being open and honest. Hurricane Harvey is an example of communication that can be used to convey a risk. The Houston region was hit hard by this devastating hurricane in 2017. Public officials used communication methods that included social media, national, as well as local media to warn affected residents to evacuate. Professionals should direct people towards reliable sources to get information.
Poor communication is a major risk when managing projects. Poor communication can lead to a project's failure. Effective communication is key to increasing employee engagement, and decreasing the chance of miscommunication. A project's management risk assessment should include activities that improve communication efforts. Once this has been done, project managers will be able to take steps in order to mitigate the risk. These include using a communication risk assessment tool, and involving stakeholders in the process.
Consultation
All stakeholders must be involved in the risk management process. The stakeholders can range from internal and external partners to stakeholders that are not directly involved in the project. To ensure that all stakeholders are fully informed about the risks and expectations, it's important to include them in the risk management process. Project teams must include all stakeholders in the risk assessment and management process to ensure that there is adequate consultation. Here are some tips for ensuring that the consultation process involves all key stakeholders.
A risk management consultant can help you prioritize risks. This is crucial because the highest-risk risks need more immediate attention, while a lower-risk risk will need a more modest remediation strategy. Consulting can help organizations determine the risks they face and devise a plan to manage them. Additionally, consultants will work with companies to develop an action program that will reduce risk and improve overall risk management.
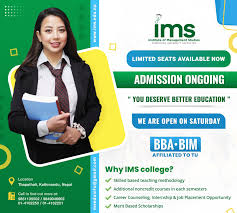
Top-down
There are some obvious advantages and disadvantages of top-down risk management. It is time-consuming, laborious, and requires expertise to implement. It is also a bespoke tool, meaning that what one manager learns in one industry might not apply to another. However, it is an excellent risk management tool. It is slowly becoming more widely accepted, even though it isn't widely used. Here are other reasons.
The initial stages of a project are the most beneficial for top-down risk management. Risk management techniques are most effective in this early phase. You can draw on the experience from previous projects. Top-down risk analysis can also contribute to managerial accountability by incorporating evidenced-based top-down risks models and techniques from past projects. Top-down risk management can reduce project risks if done correctly. Managers and teams can use them to meet their financial obligations.
FAQ
What are the key management skills?
Managerial skills are crucial for every business owner, regardless of whether they run a small store in their locality or a large corporation. They are the ability to manage people and finances, space, money, and other factors.
When you need to manage people, set goals, lead teams, motivate them, solve problems, develop policies and procedures and manage change, management skills are essential.
You can see that there are many managerial duties.
How does Six Sigma work
Six Sigma employs statistical analysis to identify problems, measure them and analyze root causes. Six Sigma also uses experience to correct problems.
The first step to solving the problem is to identify it.
Next, data are collected and analyzed in order to identify patterns and trends.
Then corrective actions are taken to solve the problem.
Finally, data will be reanalyzed to determine if there is an issue.
This cycle continues until there is a solution.
What do we mean when we say "project management"?
It refers to the management of activities related to a project.
These include planning the scope and identifying the needs, creating the budget, organizing the team, scheduling the work and monitoring progress. Finally, we close down the project.
Statistics
- Your choice in Step 5 may very likely be the same or similar to the alternative you placed at the top of your list at the end of Step 4. (umassd.edu)
- This field is expected to grow about 7% by 2028, a bit faster than the national average for job growth. (wgu.edu)
- As of 2020, personal bankers or tellers make an average of $32,620 per year, according to the BLS. (wgu.edu)
- UpCounsel accepts only the top 5 percent of lawyers on its site. (upcounsel.com)
- 100% of the courses are offered online, and no campus visits are required — a big time-saver for you. (online.uc.edu)
External Links
How To
How can you implement the Kaizen technique?
Kaizen means continuous improvement. Kaizen is a Japanese concept that encourages constant improvement by small incremental changes. It's where people work together in order to improve their processes constantly.
Kaizen is one method that Lean Manufacturing uses to its greatest advantage. The concept involves employees responsible for manufacturing identifying problems and trying to fix them before they become serious issues. This will increase the quality and decrease the cost of the products.
The main idea behind kaizen is to make every worker aware of what happens around him/her. It is important to correct any problems immediately if they are discovered. If someone spots a problem while at work, they should immediately report it to their manager.
Kaizen has a set of basic principles that we all follow. Always start with the end product in mind and work our way back to the beginning. We can improve the factory by first fixing the machines that make it. Next, we repair the machines that make components. Then, the machines that make raw materials. Then we fix the workers, who directly work with these machines.
This method, called 'kaizen', focuses on improving each and every step of the process. When we are done fixing the whole factory, we go back to the beginning and continue until we reach perfection.
It is important to understand how to measure the effectiveness and implementation of kaizen in your company. There are several ways that you can tell if your kaizen system is working. One method is to inspect the finished products for defects. Another method is to determine how much productivity has improved since the implementation of kaizen.
If you want to find out if your kaizen is actually working, ask yourself why. Was it just because it was the law or because you wanted to save money? Did you really think that it would help you achieve success?
If you answered yes to any one of these questions, congratulations! You're now ready to get started with kaizen.